Ultimate Guide to Optimizing Auto Labor Time Efficiency in Automotive Repair
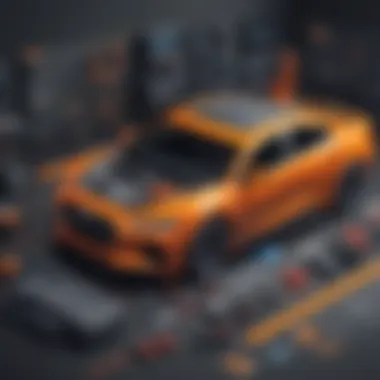
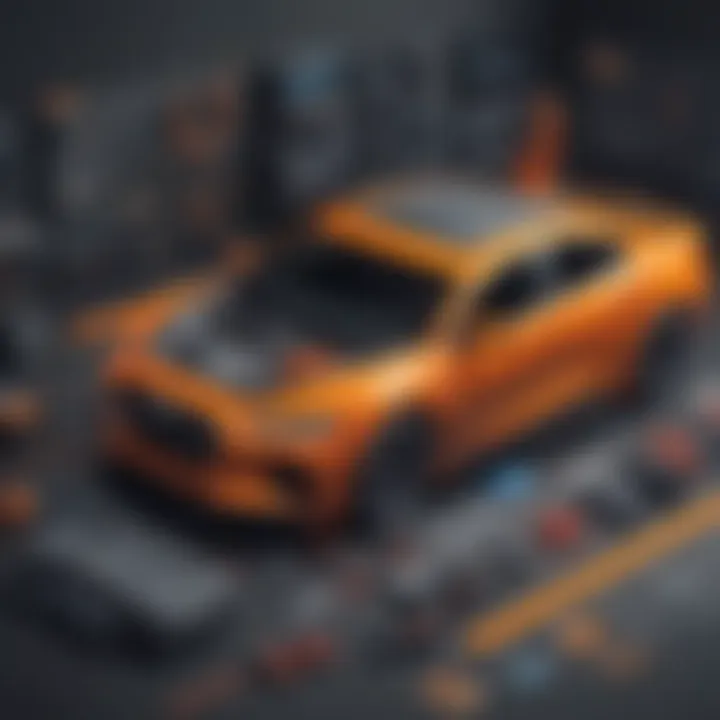
Software Overview
In the realm of automotive repair, optimizing efficiency through auto labor time management is crucial. Introducing cutting-edge software designed to revolutionize how businesses operate in this industry. This software offers a streamlined approach to managing labor time, increasing transparency, and enhancing overall productivity. The key features include automated scheduling, real-time tracking of labor hours, and data analytics for performance evaluation. Pricing plans are diverse, catering to the varied needs of small to medium-sized businesses, entrepreneurs, and IT professionals.
User Experience
Navigating through the software interface is intuitive, with user-friendly elements that facilitate seamless interaction. The learning curve is minimal, ensuring quick adoption and maximum utilization of the software's capabilities. Customer support is robust, with multiple channels available for assistance. The reliability of support services adds a layer of convenience and assurance to users seeking prompt solutions to any queries or issues they may encounter.
Performance and Reliability
The software operates with exceptional speed and efficiency, allowing for swift access to valuable data and functions. Downtime is minimal, guaranteeing uninterrupted service crucial for businesses reliant on continuous operations. Integration capabilities with other tools enhance the software's utility, promoting a cohesive workflow and interconnected system that optimizes overall performance.
Security and Compliance
Data security is paramount, and the software employs advanced encryption protocols to safeguard sensitive information. Compliance with industry regulations ensures adherence to established standards, instilling trust and confidence in users regarding data protection. Backup and disaster recovery measures are in place, providing additional layers of security and preparedness in unforeseen circumstances.
Introduction
Welcome to the intricate realm of auto labor time management in the automotive repair industry. This comprehensive guide delves into the crucial aspects of optimizing efficiency in the intricate domain of automotive repair. Understanding auto labor time is pivotal as it directly impacts operations, costs, and overall productivity for businesses and professionals in the industry. By embracing effective labor time practices, businesses can streamline their operations and enhance profitability while ensuring customer satisfaction.
Defining Auto Labor Time
Explanation of Auto Labor Time in the Automotive Industry
Auto labor time, a cornerstone in automotive repair, refers to the estimated time required to complete a specific repair or maintenance task on a vehicle. This aspect plays a vital role in service centers, allowing for precise scheduling, cost estimation, and resource allocation. The meticulous breakdown of labor time enhances operational efficiency, providing a structured approach to tackling complex repair processes. Embracing accurate labor time estimates empowers businesses to deliver prompt services and meet customer expectations efficiently.
Significance of Accurate Labor Time Estimates
The significance of accurate labor time estimates cannot be overstated in the automotive domain. Precise time estimates enable service providers to quote reasonable prices to customers, manage workflow effectively, and optimize resource allocation. By ensuring accuracy in labor time estimates, businesses can minimize delays, enhance productivity, and build a reputation for reliability and professionalism in the competitive automotive repair market. Embracing accurate labor time estimates is key to achieving operational excellence and customer satisfaction in the industry.
Industry Standards
Overview of Industry Benchmarks for Labor Time
Industry benchmarks for labor time serve as guiding principles for service centers, aligning their operations with industry best practices. These benchmarks establish standardized timeframes for common repair tasks, enabling service providers to set realistic expectations for customers and streamline workflow. Adhering to industry benchmarks facilitates transparency, consistency, and efficiency in service delivery, positioning businesses for sustainable growth and success in the dynamic automotive repair landscape.
Comparison of Different Industry Standards
Comparing different industry standards provides service centers with insights into various approaches and methodologies for estimating labor time. By examining and evaluating diverse standards, businesses can identify best-fit practices that align with their operations and objectives. Understanding the nuances of different industry standards empowers service providers to customize their labor time estimation processes, optimize workflow, and enhance overall operational efficiency. By leveraging insights from comparative analysis, businesses can stay agile and competitive in the ever-evolving automotive repair industry.
Importance of Efficiency

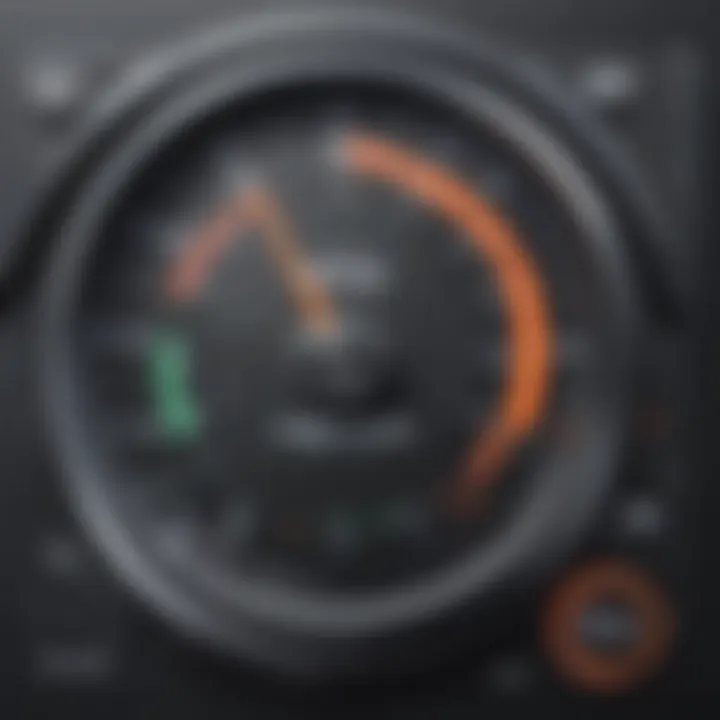
Impact of Efficient Labor Practices on Business Profitability
Efficient labor practices have a direct impact on the profitability and sustainability of automotive repair businesses. By optimizing labor processes, service providers can reduce operational costs, increase service capacity, and maximize revenue generation. Embracing efficiency in labor practices elevates the overall performance of businesses, fostering growth opportunities and long-term success in a competitive market. From improving workflow to enhancing customer satisfaction, efficient labor practices are instrumental in driving financial success and operational excellence in the automotive repair sector.
Strategies for Enhancing Efficiency in Auto Repair
Enhancing efficiency in auto repair requires a strategic approach that encompasses various aspects of operations, skills, and technology. By implementing tailored strategies such as optimized scheduling, skill development programs, and technology integration, businesses can streamline their processes and deliver exceptional service quality. Embracing continuous improvement, training initiatives, and performance evaluation enables service providers to stay ahead of industry trends, meet evolving customer demands, and maintain a competitive edge. Adopting innovative strategies for efficiency enhancement is key to unlocking the full potential of automotive repair businesses and driving sustainable growth in the dynamic market landscape.
Establishing Guidelines:
In this critical section of the article on optimizing efficiency in automotive repair, the focus shifts towards establishing guidelines that form the bedrock of effective labor time management. By delving into the intricacies of creating structured protocols, businesses can significantly enhance their operational efficiency. Understanding that meticulous guidelines pave the way for streamlined processes is paramount in the competitive landscape of auto repair. Through the establishment of clear and comprehensive guidelines, businesses empower their personnel to perform tasks efficiently and accurately, thereby boosting overall productivity.
Utilizing Software Solutions:
Benefits of using auto labor time guide software:
Exploring the benefits of integrating auto labor time guide software uncovers a world of possibilities for precision and timeliness in automotive repair processes. This software offers tailored solutions to optimize labor time calculations and streamline workflow. Its user-friendly interface and automated features contribute to minimizing errors and maximizing efficiency. The real-time data insights provided by this software become invaluable assets for informed decision-making, leading to enhanced operational performance and customer satisfaction.
Features to look for in software solutions:
Understanding the essential features to seek in software solutions for auto labor time management is pivotal for businesses aiming to excel in efficiency. From customizable labor estimates to predictive analysis capabilities, the ideal software must align with the specific needs of the business. Scalability, integration with existing systems, and robust security protocols are among the critical considerations when selecting software solutions. Balancing functionality with user-friendliness ensures seamless adoption and maximum utility for optimizing efficiency in automotive repair operations.
Creating Customized Labor Estimates:
Factors to consider when developing labor time estimates:
The process of creating labor estimates demands a meticulous approach, considering various factors that influence the duration of automotive repair tasks. By meticulously analyzing past data, skill levels of technicians, and the complexity of repairs, businesses can generate accurate and reliable labor time estimates. This tailored approach enhances cost-effectiveness and enhances operational planning, leading to improved customer service and satisfaction.
Tailoring estimates to specific repair tasks:
Tailoring labor estimates to the unique requirements of specific repair tasks is a strategic move that fosters precision and efficiency in auto repair processes. By customizing estimates based on the intricacies of each repair task, businesses optimize resource allocation and time management. This practice ensures that labor hours are allocated judiciously, increasing productivity and minimizing downtime, ultimately resulting in enhanced profitability.
Training and Skill Development:
Investing in employee training for accurate time estimation:
Investing in comprehensive employee training programs focused on accurate time estimation is a cornerstone for operational excellence in automotive repair. By enhancing the skill set of staff members in estimating labor time effectively, businesses nurture a culture of precision and expertise. Empowering employees with the tools and knowledge to calculate labor time accurately not only enhances operational efficiency but also boosts employee morale and retention rates.
Enhancing technical skills to improve efficiency:
Elevating technical skills among staff members plays a pivotal role in optimizing efficiency in auto repair processes. By focusing on continuous skill development initiatives, businesses equip their workforce with the expertise to handle tasks with proficiency and speed. The enhancement of technical skills translates into higher quality repairs, faster turnaround times, and increased customer satisfaction, positioning the business as a leader in the competitive automotive repair industry.
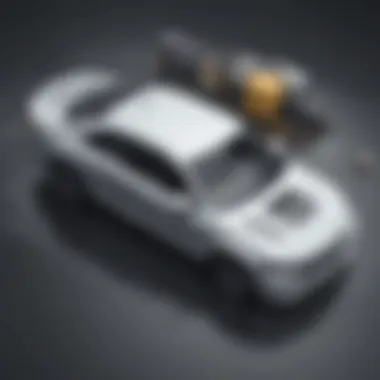
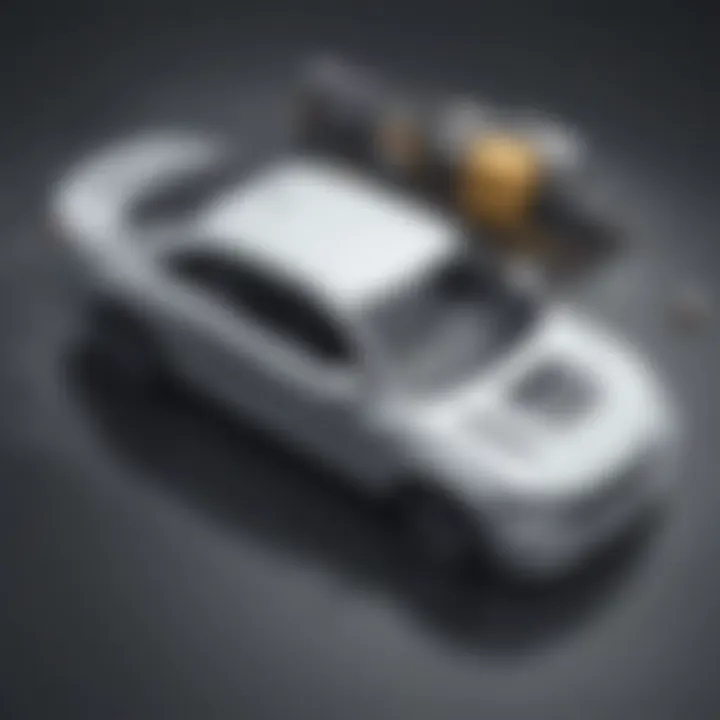
Streamlining Workflow
Optimizing Resource Allocation
Balancing workload for optimal time management
Balancing workload for optimal time management plays a central role in ensuring that business operations run smoothly and efficiently. By distributing tasks evenly among employees, businesses can prevent bottlenecks and delays, consequently streamlining the repair process. The key characteristic of balancing workload lies in its ability to optimize resource utilization, allowing businesses to meet deadlines and deliver services promptly. Despite its effectiveness, challenges may arise in accurately assessing workload distribution, requiring constant monitoring and adjustment to maintain optimal performance.
Utilizing resources efficiently
Efficient resource utilization is fundamental to maximizing productivity and minimizing waste. By ensuring that resources are allocated judiciously, businesses can enhance operational efficiency and deliver services effectively. The key characteristic of utilizing resources efficiently is the ability to streamline processes and eliminate unnecessary expenditures. However, challenges such as resource scarcity or inadequate tools may hinder optimal resource utilization, necessitating proactive solutions to overcome obstacles and maintain operational excellence.
Implementing Time-Saving Techniques
Strategies for reducing repair time without compromising quality
Efficiently reducing repair time without compromising quality is a delicate balance that requires strategic planning and meticulous execution. By implementing smart scheduling practices and optimizing workflow sequences, businesses can minimize downtime and enhance service delivery. The key characteristic of these strategies is their focus on achieving time efficiency without sacrificing the quality of repairs. While effective, challenges such as unexpected complications or client demands may pose obstacles, necessitating swift adaptation and proactive problem-solving to uphold service standards.
Maximizing output through efficient workflow
Maximizing output through efficient workflow is a core strategy for increasing productivity and maximizing resource utilization. By streamlining processes and optimizing task allocation, businesses can accelerate service delivery without compromising quality. The key characteristic of this approach lies in its ability to boost overall output while maintaining operational efficiency. Challenges such as workforce fluctuations or equipment malfunctions may affect workflow efficiency, highlighting the need for contingency plans and dynamic resource management to sustain high performance.
Monitoring and Evaluation
Importance of tracking labor time data
Tracking labor time data is crucial for assessing operational efficiency and identifying areas for improvement. By analyzing time allocation and task completion rates, businesses can pinpoint bottlenecks and streamline processes effectively. The key characteristic of tracking labor time data is its role in providing actionable insights for enhancing workflow efficiency. Despite its benefits, challenges such as data accuracy or integration issues may impede the effectiveness of tracking, necessitating robust data management systems and regular audits to ensure reliable performance.
Analyzing performance indicators for continuous improvement
Analyzing performance indicators is essential for driving continuous improvement and maintaining operational excellence. By evaluating key metrics such as service completion times and customer satisfaction ratings, businesses can identify trends and adapt strategies accordingly. The key characteristic of analyzing performance indicators lies in its ability to foster a culture of innovation and adaptability. However, challenges such as data interpretation or metric relevance may impact the effectiveness of analysis, highlighting the need for dynamic evaluation frameworks and ongoing skill development to leverage performance data effectively.
Ensuring Accuracy
Ensuring accuracy in automotive repair processes is crucial for maintaining high standards of efficiency and quality. In the context of this article about optimizing auto labor time, accuracy plays a pivotal role in enhancing overall business productivity and customer satisfaction. By focusing on precise labor time estimates, repair shops can establish a reputation for reliability and professionalism. Furthermore, accurate calculations lead to optimal resource allocation, reducing wastage and maximizing profitability. Through a meticulous approach to accuracy, businesses can streamline operations and improve their competitive edge within the industry.
Quality Control Processes
Implementing checks to ensure accurate labor time estimates
Implementing checks to ensure accurate labor time estimates involves establishing robust mechanisms to verify the time required for automotive repair tasks. By implementing thorough inspection procedures and standardized assessment criteria, businesses can mitigate the risk of errors and discrepancies in labor time calculations. This meticulous approach enhances the credibility of labor estimates and instills customer confidence in the service provider. The key characteristic of this quality control process is its ability to identify and rectify inaccuracies promptly, ensuring that the final labor time figures are precise and reliable. Implementing checks to ensure accurate labor time estimates is a popular choice for this article due to its direct impact on operational efficiency and business reputation. While the process may require initial investment in terms of time and resources, the long-term benefits of increased accuracy and customer satisfaction make it a valuable strategy for automotive repair businesses.

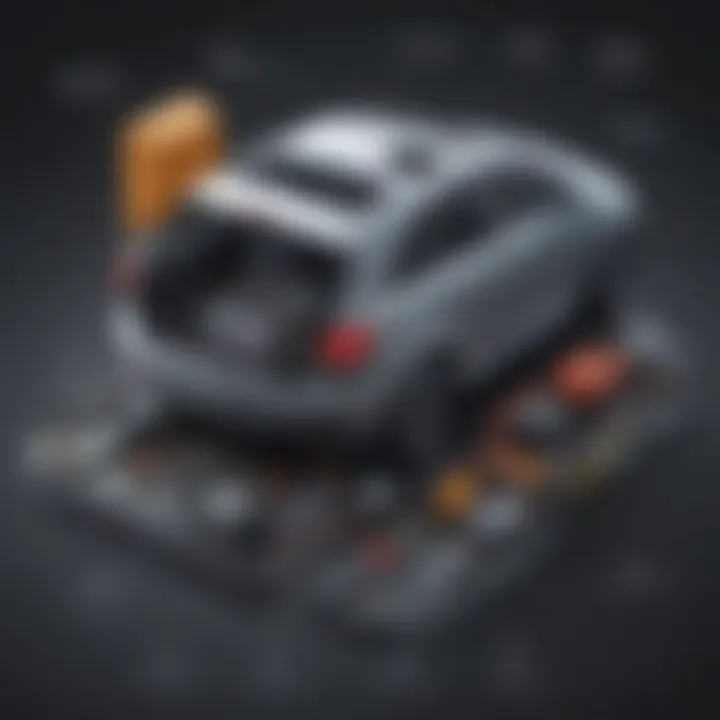
Addressing discrepancies proactively
Addressing discrepancies proactively involves preemptive problem-solving to resolve potential issues before they impact service delivery. By monitoring labor time estimates closely and conducting regular audits, businesses can identify discrepancies early and take corrective action efficiently. This proactive approach minimizes disruptions to workflow and ensures that customers receive timely and accurate repair services. The unique feature of addressing discrepancies proactively lies in its preventive nature, whereby businesses actively seek out and address potential errors before they escalate. While this strategy requires ongoing vigilance and attention to detail, its advantages in terms of customer retention and operational smoothness are significant. Addressing discrepancies proactively aligns with the objectives of this article by emphasizing the importance of maintaining accuracy and consistency in labor time estimation to drive business success.
Feedback Mechanisms
Collecting feedback from technicians for refinement
Collecting feedback from technicians for refinement involves soliciting input from frontline staff regarding the accuracy and efficiency of labor time estimates. By leveraging the experiential knowledge of technicians who perform repair tasks, businesses can gain valuable insights into potential areas for improvement. This collaborative approach empowers technicians to contribute to the enhancement of labor time estimation processes and fosters a culture of continuous improvement within the organization. The key characteristic of collecting feedback from technicians for refinement is its ability to incorporate real-world feedback into operational decision-making, leading to more accurate labor time predictions. This practice is a beneficial choice for this article as it underscores the significance of internal expertise in refining accuracy and streamlining workflow processes. Despite potential challenges in collecting and analyzing feedback effectively, the benefits of improved precision in labor time estimation justify the effort invested in this feedback mechanism.
Iterative processes for continuous accuracy
Iterative processes for continuous accuracy involve ongoing refinement and adjustment of labor time estimation methodologies based on feedback and performance evaluation. By embracing a cycle of assessment, implementation, and reassessment, businesses can adapt to changing industry dynamics and customer requirements swiftly. This iterative approach fosters a culture of adaptability and responsiveness, enabling organizations to stay ahead of competition and deliver exceptional service quality. The unique feature of iterative processes for continuous accuracy is their flexibility and scalability, allowing businesses to refine their labor time estimation strategies iteratively to meet evolving needs. While implementing iterative processes may require a shift in organizational mindset towards continuous improvement, the benefits of enhanced accuracy and efficiency make it a strategic choice for this article. By emphasizing the importance of adaptability and learning from past experiences, iterative processes align with the objectives of optimizing efficiency in automotive repair, positioning businesses for sustained success.
Auditing and Compliance
Adhering to industry regulations and standards
Adhering to industry regulations and standards involves upholding legal requirements and best practices governing labor time estimation and service delivery in the automotive repair sector. By ensuring compliance with regulatory frameworks and industry guidelines, businesses can safeguard their reputation and mitigate risks associated with non-compliance. The key characteristic of adhering to industry regulations and standards is its role in promoting transparency and accountability in labor time estimation processes, enhancing customer trust and loyalty. This adherence to standards is a popular choice for this article as it underlines the commitment to ethical business conduct and quality assurance within the industry. While maintaining compliance may involve regular training and monitoring to stay abreast of evolving regulations, the benefits of regulatory alignment in terms of credibility and operational integrity justify the efforts invested in this aspect.
Conducting regular audits for compliance
Conducting regular audits for compliance involves systematic reviews of labor time estimation practices and operational procedures to ensure adherence to regulatory and industry standards. By conducting thorough assessments and performance evaluations, businesses can identify areas of improvement and address potential non-compliance issues proactively. This structured approach enhances operational efficiency and minimizes the risk of regulatory violations or customer disputes. The unique feature of conducting regular audits for compliance lies in its emphasis on procedural adherence and quality control, fostering a culture of accountability and continual improvement. While regular audits may require dedicated resources and time commitments, the benefits of maintaining compliance and operational excellence make them a strategic choice for this article. By prioritizing quality assurance and regulatory alignment, businesses can differentiate themselves in a competitive market and build trust among customers and industry stakeholders.
Conclusion
Optimizing efficiency in automotive repair through auto labor time management is a crucial aspect that demands attention. By implementing strategies to streamline workflow and ensure accuracy in labor estimates, businesses can significantly enhance their overall performance and profitability. This article serves as a comprehensive guide to navigating the complexities of auto labor time, equipping professionals with the necessary knowledge to make informed decisions that positively impact their operations.
Key Takeaways
Summary of key strategies for optimizing auto labor time
Exploring the key strategies for optimizing auto labor time unveils a range of effective techniques that can revolutionize how repair tasks are approached. From utilizing advanced software solutions to implementing customized labor estimates tailored to specific repair tasks, each strategy plays a pivotal role in enhancing efficiency and productivity. By understanding these strategies in depth, professionals can strategize effectively to improve their performance.
Final thoughts on enhancing efficiency in automotive repair
Delving into the final thoughts on enhancing efficiency in automotive repair emphasizes the importance of continuous improvement and adaptation in the industry. By incorporating feedback mechanisms and quality control processes into daily operations, businesses can proactively address challenges and refine their processes for better outcomes. This holistic approach towards efficiency not only boosts performance but also fosters a culture of innovation and excellence.
Future Trends
Anticipated developments in labor time management
The anticipated developments in labor time management underscore the evolution of processes and technologies within the automotive repair sector. As industry standards continue to shift towards automation and digitization, professionals must stay abreast of these changes to remain competitive. Embracing advancements like AI-driven solutions and predictive analytics can revolutionize how labor time is managed, offering unprecedented accuracy and efficiency.
Adapting to technological advancements in the industry
Adapting to technological advancements in the industry is paramount for businesses looking to stay ahead of the curve. By harnessing the power of cutting-edge tools and innovations, professionals can optimize their operations and enhance customer satisfaction. From leveraging IoT devices for real-time monitoring to integrating cloud-based systems for seamless collaboration, technological advancements present boundless opportunities for growth and success in the automotive repair landscape.