Cost Optimization Strategies for Fishbowl Inventory Management
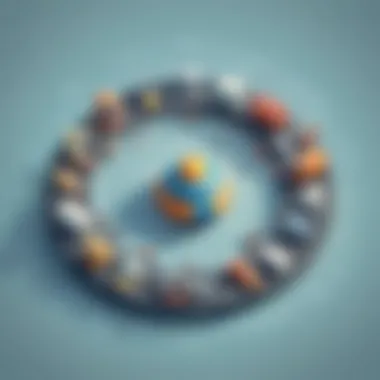

Software Overview
When considering the intricacies of optimizing fishbowl inventory cost, a comprehensive software solution becomes crucial for effective management. This section provides insights into the software designed to streamline inventory processes, enhance efficiency, and reduce costs. By offering an introduction to the software, outlining key features and functionalities tailored for fishbowl inventory management, as well as detailing pricing plans and available subscription options, businesses can make informed decisions on selecting the right tool to optimize their inventory cost control.
User Experience
User experience plays a pivotal role in ensuring the seamless integration of a software solution for fishbowl inventory cost optimization. Delving into the user interface and navigational elements of the software, this section assesses the ease of use and learning curve associated with its implementation. Furthermore, it highlights the customer support options provided, evaluating the reliability of assistance and guidance available to users navigating through the system, thereby enhancing the overall user experience.
Performance and Reliability
Efficiency and reliability are paramount when selecting a software solution for fishbowl inventory cost optimization. This section focuses on evaluating the speed and efficiency of the software in managing inventory processes, along with uptime and downtime statistics crucial for uninterrupted operations. Additionally, integration capabilities with other tools are explored to gauge the software's compatibility and adaptability within existing inventory management frameworks, ensuring a seamless and efficient performance.
Security and Compliance
Ensuring data security and compliance standards are met is essential for safeguarding sensitive information within fishbowl inventory systems. This section delves into the data encryption and security protocols implemented by the software to safeguard critical inventory data. Moreover, it examines the software's compliance with industry regulations, providing businesses with the assurance of meeting legal requirements. Backup and disaster recovery measures are also scrutinized to guarantee the resilience and continuity of inventory management operations, elevating the overall security and compliance standards of the software solution.
Understanding Fishbowl Inventory Cost
In the realm of business operations, comprehending the intricacies of fishbowl inventory cost holds paramount significance. It serves as the bedrock for effective cost management and financial prudence within companies. By gaining a deep understanding of fishbowl inventory cost, businesses can strategically optimize their resources, enhance profitability, and thrive in competitive markets. The nuances of cost analysis, valuation methods, and cost drivers are essential components encapsulated within the domain of fishbowl inventory cost. This section explores the foundational pillars of understanding fishbowl inventory cost, shedding light on its pivotal role in sustainable business practices.
Key Concepts of Fishbowl Inventory Cost
Inventory Valuation Methods
Delving into the domain of fishbowl inventory cost unveils the critical importance of inventory valuation methods. The selection of an appropriate valuation method significantly impacts financial statements, tax obligations, and business decision-making processes. FIFO (First-In-First-Out), LIFO (Last-In-First-Out), and Weighted Average Cost are popular valuation methods that play a crucial role in determining the cost of goods sold and inventory value. Understanding the nuances of each valuation method equips businesses with the necessary knowledge to make informed financial decisions tailored to their unique needs.
Cost Drivers in Fishbowl Inventory
Within the realm of fishbowl inventory cost, cost drivers act as the catalysts influencing overall expenditure. Raw material costs, labor expenses, and transportation costs emerge as pivotal elements shaping the financial landscape of businesses. By identifying and analyzing these core cost drivers, companies can streamline their cost structures, identify areas for optimization, and bolster cost-efficiency. Proactive management of cost drivers lays the groundwork for sustainable financial performance and strategic growth within a competitive market environment.
Impact of Holding Costs
The impact of holding costs on fishbowl inventory operations cannot be understated. Holding costs encompass various expenses incurred during the storage and maintenance of inventory, including warehousing expenses, insurance costs, and depreciation. Understanding the implications of holding costs enables businesses to evaluate the financial implications of inventory management, minimize unnecessary expenditures, and enhance operational efficiency. By mitigating the adverse effects of holding costs, companies can optimize their working capital, improve cash flow, and achieve sustainable growth in the long run.
Challenges in Managing Fishbowl Inventory Costs
Navigating the complexities of managing fishbowl inventory costs presents a myriad of challenges for businesses striving for operational excellence. Seasonal variations in costs, overhead expenses, and obsolete inventory issues pose significant hurdles that necessitate adept financial management strategies. By acknowledging and addressing these challenges effectively, companies can fortify their financial health, streamline operations, and stay resilient in dynamic market conditions.
Seasonal Variations in Costs
Seasonal fluctuations in costs present a substantial challenge for organizations engaged in fishbowl inventory management. The variability in demand, production cycles, and market trends during different seasons can disrupt cost structures and inventory planning efforts. Mitigating the impact of seasonal variations requires robust forecasting, strategic inventory planning, and agile supply chain management practices. By proactively addressing seasonal cost changes, businesses can optimize resource allocation, minimize financial risks, and capitalize on market opportunities.
Overhead Costs
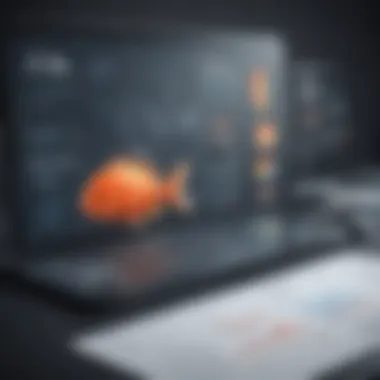

Overhead costs represent a significant component of fishbowl inventory expenses, encompassing various indirect expenses essential for business operations. Rent, utilities, administrative salaries, and other overhead expenditures can substantially impact the overall cost structure of businesses. Managing overhead costs efficiently requires diligent cost control measures, operational optimization, and strategic resource allocation. By reducing unnecessary overhead expenditures, companies can enhance cost-effectiveness, improve profitability, and strengthen their competitive position in the market.
Obsolete Inventory Expenses
The presence of obsolete inventory within fishbowl inventory systems poses a formidable challenge for businesses, leading to financial losses, storage inefficiencies, and operational bottlenecks. Obsolete inventory issues arise due to product obsolescence, changing market trends, or inaccurate demand forecasting. Effectively managing obsolete inventory expenses demands proactive inventory monitoring, timely disposition strategies, and accurate demand forecasting practices. By minimizing obsolete inventory risks, companies can unlock valuable warehouse space, improve inventory turnover rates, and optimize cost structures for sustained profitability.
Analyzing Fishbowl Inventory Cost Drivers
Analyzing Fishbowl Inventory Cost Drivers is a pivotal aspect within this comprehensive guide on Optimizing Fishbowl Inventory Cost. Understanding the various cost drivers allows businesses to delve deep into the core elements influencing their inventory expenses. It sheds light on the critical areas such as raw material costs, labor expenses, and transportation costs, offering a holistic view of the financial aspects affecting inventory management. By scrutinizing these drivers, organizations can pinpoint optimization opportunities, identify areas of improvement, and enhance cost-efficiency.
Direct vs. Indirect Costs
Raw Material Costs
Raw Material Costs play a fundamental role in the overall inventory cost structure. They encompass expenses associated with procuring essential materials for production. The significance of Raw Material Costs lies in their direct impact on the final product cost and, consequently, profit margins. Businesses must carefully monitor raw material expenses to ensure optimal cost-effectiveness. While fluctuations in raw material prices can pose challenges, managing and forecasting these costs diligently can lead to cost savings and competitive pricing advantages.
Labor Expenses
Labor Expenses constitute a crucial component of overall inventory costs, encompassing the wages and benefits of personnel involved in manufacturing and warehouse operations. The efficiency of labor utilization directly influences production costs and operational efficiency. Optimizing labor expenses involves streamlining processes, enhancing workforce productivity, and implementing lean manufacturing principles. By addressing labor costs effectively, businesses can boost cost efficiencies, streamline operations, and improve profitability.
Transportation Costs
Transportation Costs play a vital role in the supply chain, encompassing expenses related to shipping, freight, and logistics. Their role in inventory management is critical as they impact product lead times, order fulfillment speed, and overall operational costs. Efficient transportation cost management involves optimizing shipping routes, leveraging economies of scale through bulk transportation, and negotiating favorable freight rates. By optimizing transportation costs, businesses can enhance supply chain efficiency, reduce delivery lead times, and lower overall logistics expenses.
Strategies for Optimizing Fishbowl Inventory Costs:
In the context of this comprehensive guide on optimizing fishbowl inventory costs, the section on strategies for cost optimization plays a pivotal role. Understanding and implementing effective strategies can significantly impact a business's profitability and operational efficiency. By focusing on specific elements such as forecasting, demand planning, and inventory management techniques, businesses can streamline operations and reduce unnecessary expenses. These strategies are fundamental in navigating the complexities of fishbowl inventory management, offering insights into enhancing profit margins, improving cash flow, and developing competitive pricing strategies.
Forecasting and Demand Planning:
Utilizing Historical Data:
When it comes to optimizing fishbowl inventory costs, leveraging historical data is a critical aspect of forecasting and demand planning. By harnessing past trends and patterns in sales, businesses can make informed decisions regarding inventory levels and procurement strategies. The key characteristic of utilizing historical data lies in its ability to provide a reliable foundation for future projections, aiding businesses in anticipating demand fluctuations and minimizing stockouts. Despite its benefits, one must also consider the potential limitations of historical data, such as its susceptibility to changes in market dynamics that may render certain past trends obsolete.
Collaborative Planning with Suppliers:
Collaborative planning with suppliers is another integral component of effective forecasting and demand planning. By fostering a transparent and communicative relationship with suppliers, businesses can ensure a smooth flow of inventory while minimizing holding costs. The key characteristic of this approach is the emphasis on mutual trust and cooperation between parties, leading to optimized lead times and reduced risks of stockouts. However, businesses must also be wary of overdependence on suppliers and the potential challenges of aligning goals and strategies.
Implementing Just-in-Time Inventory:
Implementing a just-in-time inventory system is a proactive strategy to optimize fishbowl inventory costs. By synchronizing inventory levels with actual demand, businesses can reduce excess inventory and associated holding costs. The key characteristic of just-in-time inventory lies in its focus on efficiency and waste reduction, allowing businesses to operate with leaner inventories and streamlined operations. Despite its advantages, businesses must consider the risks of supply chain disruptions and the need for robust contingency plans to mitigate potential disruptions.
Effective Inventory Management Techniques:
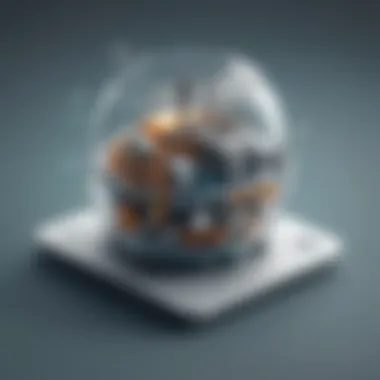

ABC Analysis:
ABC analysis is a valuable technique in optimizing fishbowl inventory costs by categorizing items based on their value and importance. By prioritizing inventory management according to the Pareto principle, businesses can allocate resources efficiently and focus on high-value items. The key characteristic of ABC analysis lies in its ability to classify items into different categories, facilitating targeted inventory control strategies. While advantageous in optimizing costs, businesses must also consider the time and resources required for frequent classification updates and adaptability to shifting market demands.
Batch Tracking:
Batch tracking is an essential inventory management technique that enables businesses to monitor and trace specific batches of products throughout the supply chain. By assigning unique identifiers to batches, businesses can enhance product quality control, recall management, and expiration tracking. The key characteristic of batch tracking is its emphasis on traceability and compliance with regulatory standards, ensuring product visibility and accountability. Despite its benefits, businesses must address the complexities of batch identification and integration with existing inventory systems.
Cycle Counting:
Cycle counting is a methodical approach to inventory management that involves regular and systematic counts of subsets of inventory items. By conducting frequent cycle counts, businesses can identify discrepancies, minimize errors, and maintain accurate inventory records. The key characteristic of cycle counting is its emphasis on continuous monitoring and real-time accuracy, providing insights into inventory discrepancies and operational inefficiencies. While beneficial in optimizing inventory costs, businesses must allocate resources and training effectively to implement a successful cycle counting program.
Utilizing Technology for Cost Optimization:
Inventory Management Software:
In the realm of cost optimization for fishbowl inventory, the adoption of inventory management software is instrumental in enhancing efficiency and accuracy. By leveraging advanced software solutions, businesses can automate inventory tracking, streamline order processing, and generate real-time reports. The key characteristic of inventory management software is its comprehensive functionality, encompassing inventory control, forecasting, and performance analytics. While advantageous in improving operational workflows, businesses must also consider the initial investment costs and the learning curve associated with software integration.
Automated Reorder Points:
Automated reorder points are a strategic tool in optimizing fishbowl inventory costs by establishing predetermined triggers for inventory replenishment. By setting automated reorder points based on demand forecasting and lead times, businesses can mitigate stockouts and prevent excess inventory buildup. The key characteristic of automated reorder points is their capacity to streamline replenishment processes and reduce manual intervention, leading to seamless inventory management. However, businesses must ensure accurate data inputs and regular adjustments to avoid understocking or overstocking scenarios.
Integration with Accounting Systems:
Efficient integration with accounting systems is paramount in optimizing fishbowl inventory costs by aligning financial records with inventory transactions. By synchronizing inventory data with accounting platforms, businesses can enhance visibility into cost structures, profitability analysis, and financial reporting. The key characteristic of integration with accounting systems is its facilitation of seamless data flow and cross-functional collaboration between inventory management and financial departments. While beneficial in promoting data accuracy and operational efficiency, businesses must address potential compatibility issues and data security concerns during the integration process.
Implementing Cost-Effective Measures
In this section of the guide on Optimizing Fishbowl Inventory Cost, implementing cost-effective measures plays a pivotal role in enhancing operational efficiency and cost optimization for businesses. By focusing on specific elements such as supplier relationships, order consolidation, and operational streamlining, companies can significantly reduce expenses and improve profit margins. The benefits of implementing cost-effective measures include better cost control, enhanced supplier collaboration, and overall cost savings. Businesses need to consider factors such as negotiation strategies, order management systems, and vendor partnerships to achieve sustainable cost savings and operational excellence.
Supplier Relationship Management
Supplier relationship management is crucial for maximizing cost-effectiveness in fishbowl inventory management. By fostering strong ties with suppliers, businesses can secure favorable terms, discounts, and efficient order fulfillment processes. Through effective supplier relationship management, companies can negotiate volume discounts, consolidate orders, and establish long-term partnerships to streamline procurement and reduce costs. Leveraging supplier relationships fosters trust, transparency, and reliability in the supply chain, leading to mutual benefits for both parties.
Negotiating Volume Discounts
Negotiating volume discounts is a key aspect of supplier relationship management that offers significant cost-saving opportunities for businesses. By committing to large purchase volumes, companies can negotiate lower unit costs, resulting in overall cost reduction. The key characteristic of negotiating volume discounts lies in the ability to scale procurement volume while ensuring quality standards and delivery timelines. This approach is beneficial for businesses looking to optimize their purchasing power and drive down material costs, ultimately enhancing their bottom line.
Consolidating Orders
Consolidating orders involves combining multiple purchase requests into a single transaction to leverage economies of scale and reduce transactional costs. This practice streamlines the procurement process, reduces supplier overheads, and enhances order accuracy. The unique feature of consolidating orders lies in its ability to minimize administrative efforts, standardize procurement workflows, and maximize cost efficiencies. While consolidating orders offers cost-saving advantages, businesses need to strike a balance between volume consolidation and inventory holding costs.
Establishing Vendor Partnerships
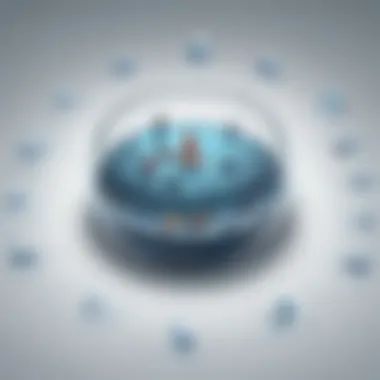

Establishing strong vendor partnerships is vital for optimizing cost-effective measures in fishbowl inventory management. By collaborating closely with trusted suppliers, businesses can enhance supply chain visibility, access new market opportunities, and drive innovation. The key characteristic of vendor partnerships is the development of mutually beneficial relationships based on trust, shared goals, and continuous improvement. Building strategic vendor partnerships enables businesses to reduce lead times, customize inventory solutions, and mitigate supply chain risks effectively.
Streamlining Operations for Efficiency
Efficient operational processes are fundamental to reducing costs and improving productivity in fishbowl inventory management. By streamlining operations for efficiency, businesses can optimize order fulfillment, minimize lead times, and prevent stockouts. This strategic approach enhances overall operational agility, customer satisfaction, and cost competitiveness. Companies need to focus on optimizing order fulfillment, reducing lead times, and minimizing stockouts to sustain operational excellence and cost efficiency.
Optimizing Order Fulfillment
Optimizing order fulfillment involves ensuring timely and accurate processing of customer orders to meet demand forecasts efficiently. By improving order processing workflows, inventory visibility, and shipping practices, businesses can enhance customer satisfaction and reduce fulfillment costs. The key characteristic of optimizing order fulfillment is the alignment of inventory levels with customer demand, enabling just-in-time deliveries and inventory replenishment. This practice ensures swift order processing, inventory turnover, and fulfillment accuracy, leading to cost savings and customer loyalty.
Reducing Lead Times
Reducing lead times is essential for minimizing process inefficiencies, enhancing supply chain responsiveness, and meeting customer demand promptly. By implementing lean practices, inventory optimization techniques, and process automation, businesses can shorten lead times and improve operational efficiency. The unique feature of reducing lead times lies in its ability to accelerate order processing, manufacturing cycles, and delivery schedules. While reducing lead times offers competitive advantages, companies need to balance speed with quality, cost-effectiveness, and inventory management to achieve sustainable operational improvements.
Minimizing Stockouts
Minimizing stockouts is critical for preventing revenue losses, maintaining customer satisfaction, and optimizing inventory turnover rates. By implementing inventory monitoring systems, demand forecasting tools, and safety stock strategies, businesses can avoid stockouts and mitigate supply chain disruptions. The key characteristic of minimizing stockouts is the proactive management of inventory levels, reorder points, and supplier lead times to meet fluctuating demand effectively. This practice ensures business continuity, customer retention, and competitive positioning in the market.
Measuring Success and Continuous Improvement
Measuring success and continuous improvement are pivotal aspects of effective fishbowl inventory cost management. In this article, we delve into the essential strategies to gauge performance and drive ongoing enhancements. By meticulously analyzing key performance indicators (KPIs), businesses can fine-tune their operations for better outcomes. Evaluating success enables businesses to identify areas of strength and opportunities for refinement, ensuring sustainable growth and profitability.
Key Performance Indicators for Cost Management
Inventory Turnover Ratio
Inventory turnover ratio is a critical metric within cost management, shedding light on how efficiently a company utilizes its inventory. This ratio highlights the frequency with which a business sells and replaces inventory within a specific period. A high turnover ratio indicates effective inventory management, minimizing holding costs and enhancing cash flow. However, excessively high turnover may lead to stockouts and lost sales. Properly interpreting and acting upon this indicator is vital for maintaining a healthy balance between carrying costs and sales revenue.
Carrying Costs as a Percentage of Inventory Value
Carrying costs as a percentage of inventory value offer insights into the expenses associated with holding stock. This metric considers expenses like warehousing, depreciation, insurance, and obsolescence relative to the total inventory value. By monitoring this KPI, businesses can optimize inventory levels to reduce unnecessary costs while ensuring adequate stock availability. Lowering carrying costs boosts financial performance and competitiveness, emphasizing the need for precise calculation and continuous assessment to drive informed cost-saving decisions.
Order Fulfillment Accuracy
Order fulfillment accuracy reflects the efficiency and reliability of a company's order processing and delivery operations. Maintaining high accuracy levels is crucial for customer satisfaction, repeat business, and overall cost management. Accurate order fulfillment minimizes returns, rework, and associated expenses, bolstering operational efficiency and profitability. Investing in technologies and processes to enhance accuracy optimizes workflows, reduces costs, and cements customer loyalty, underscoring the significance of this KPI in shaping overall business success.
Iterative Strategies for Ongoing Optimization
Regular Cost Reviews and Analysis
Continuous cost reviews and analysis form the cornerstone of ongoing optimization in fishbowl inventory management. Regularly scrutinizing expenses, trends, and performance metrics enables businesses to detect cost-saving opportunities and operational efficiencies. By conducting in-depth analyses, companies can identify areas for improvement, implement targeted cost-cutting measures, and adapt to evolving market demands. Vigilant monitoring and proactive decision-making based on analytical insights drive sustainable cost reductions and operational excellence.
Feedback Loops for Process Enhancement
Implementing feedback loops for process enhancement fosters a culture of continuous improvement within organizations. Feedback mechanisms allow businesses to gather insights from stakeholders, customers, and internal teams, facilitating informed decisions and process refinements. Incorporating feedback loops ensures responsiveness to changing market dynamics, customer preferences, and operational challenges. This iterative approach nurtures innovation, fosters agility, and enables swift adjustments to enhance cost-effectiveness and customer satisfaction.
Incorporating Employee Training on Cost Awareness
Employee training on cost awareness cultivates a cost-conscious environment where staff understand the impact of their actions on business expenses. Educating employees on cost drivers, budget adherence, and efficiency measures empowers them to contribute directly to cost optimization efforts. By instilling a culture of accountability and resourcefulness, companies can drive continuous cost-aware behaviors across all departments. Investing in employee training enhances overall cost management capabilities, aligns teams with organizational goals, and positions businesses for sustained financial success.