Optimizing Efficiency in Automotive Repair Shops with Real-Time Auto Labor Guide
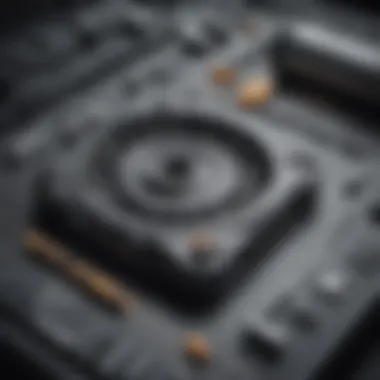
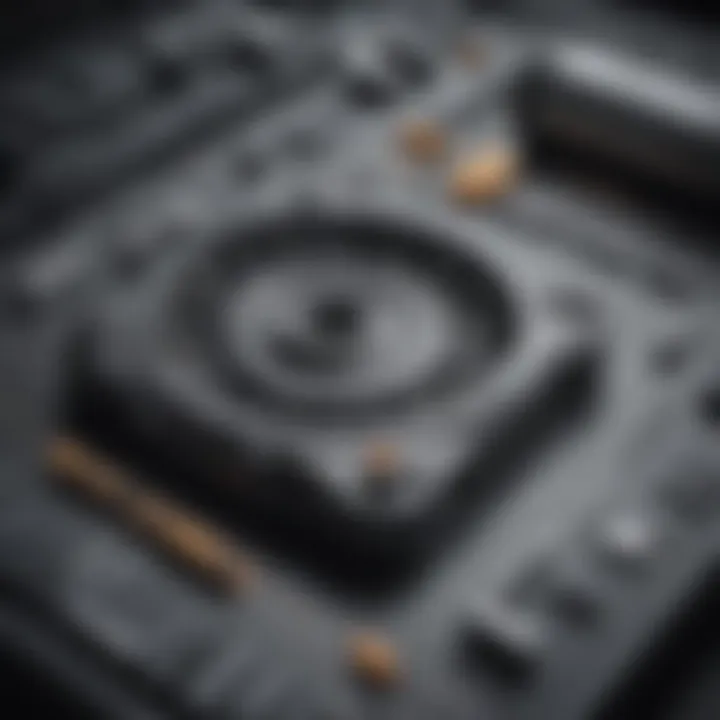
Software Overview
The realm of automotive repair shops is evolving rapidly, with the integration of real-time auto labor guides proving to be a game-changer in optimizing efficiency and streamlining operations. These innovative software solutions offer a comprehensive breakdown of labor costs, precise time estimations, and encapsulate best practices within the automotive repair industry. By harnessing the power of technology, repair shop owners can revolutionize their workflow and enhance overall productivity.
User Experience
When delving into the realm of real-time auto labor guides, one of the key aspects that demand attention is the user experience. These software solutions boast intuitive user interfaces that simplify complex tasks, allowing even novice users to navigate with ease. From seamless navigational elements to a minimal learning curve, these guides prioritize user-friendliness to ensure a smooth and efficient experience. Additionally, robust customer support options further enhance reliability, ensuring that users can avail of timely assistance and troubleshooting when required.
Performance and Reliability
The performance and reliability standards set by real-time auto labor guides are paramount in determining their efficacy within automotive repair shops. These cutting-edge solutions are designed to deliver unparalleled speed and efficiency, enabling users to streamline their operations seamlessly. With impressive uptime statistics and minimal downtime, these guides ensure uninterrupted access to critical resources. Moreover, their integration capabilities with other tools serve to enhance synergy within the shop’s existing infrastructure, fostering a harmonious workflow.
Security and Compliance
Security is a top priority in the automotive repair industry, and real-time auto labor guides deliver on this front with stringent data encryption protocols and robust security measures. These software solutions adhere to industry regulations, ensuring compliance and data integrity. Furthermore, backup and disaster recovery mechanisms safeguard against unforeseen contingencies, providing peace of mind to shop owners and technicians alike.
Introduction
In the realm of automotive repair shops, efficiency is a pivotal element that can make or break the success of the business. The introduction of a real-time auto labor guide offers a revolutionary approach to optimizing workflow and boosting operational efficiency within the automotive industry. By delving into the intricacies of labor costs, time estimation methodologies, and best practices, this guide aims to streamline processes, improve resource allocation, and ultimately enhance the overall performance of repair shops.
Understanding Real-Time Auto Labor Guide
Definition and Purpose
The core essence of a real-time auto labor guide lies in its ability to provide accurate and dynamic guidance in labor cost estimations and time assessments within automotive repair settings. This crucial tool serves as a compass for technicians, offering detailed insights into the required tasks, timelines, and necessary resources for efficient repairs. The unique selling point of this system is its real-time nature, enabling on-the-spot adjustments and ensuring precision in cost estimations, enhancing the decision-making process for both technicians and shop owners.
Benefits of Implementing
Implementing a real-time auto labor guide brings a plethora of advantages to the forefront of automotive repair shops. One key benefit is the improved accuracy and transparency it offers in cost estimations, fostering trust and loyalty among customers. Additionally, this system enhances operational efficiency by providing technicians with clear guidelines and estimates, thus reducing wastage of time and resources. The dynamic nature of real-time monitoring and updates ensures adaptability to changing circumstances, further optimizing the repair process.
Evolution of Labor Guides in the Automotive Industry
The evolution of labor guides within the automotive industry has been marked by a gradual shift towards more technology-driven solutions. Traditional methods of manual labor estimation have given way to sophisticated predictive algorithms and historical data utilization for enhanced accuracy. This evolution underscores the industry's commitment to staying abreast of technological advancements, aiming to improve overall efficiency and customer satisfaction through advanced labor guide systems.
Significance of Efficiency in Automotive Repair
Key Metrics for Operational Success
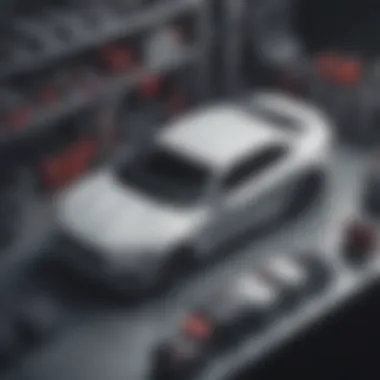
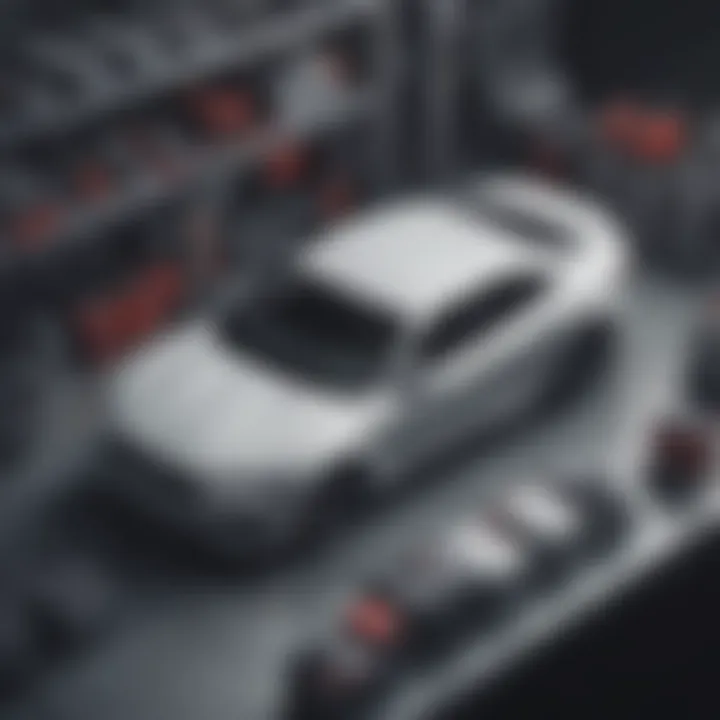
Efficiency in automotive repair hinges on the meticulous monitoring of key performance metrics that directly impact operational success. These metrics encompass factors like turnaround time, resource allocation efficiency, and technician productivity. By rigorously tracking these indicators, repair shops can identify areas for improvement, optimize processes, and ultimately elevate the quality of services provided to customers.
Challenges Faced Without Proper Time Estimation
One of the primary challenges faced by automotive repair shops in the absence of proper time estimation is the risk of underestimating or overestimating labor requirements for a given task. This can lead to delays in service delivery, decreased customer satisfaction, and increased operational costs. Accurate time estimation is crucial for effective scheduling, resource allocation, and overall workflow coordination within repair shops.
Impact on Customer Satisfaction
Proper time estimation plays a pivotal role in shaping customer satisfaction levels within automotive repair shops. Timely service delivery, accurate cost estimates, and efficient resource utilization directly contribute to the overall customer experience. By implementing effective time estimation practices, repair shops can build trust, foster loyalty, and establish a reputation for reliability and professionalism among their clientele.
Components of an Effective Auto Labor Guide
In the landscape of automotive repair shops, having an effective auto labor guide is paramount for optimizing efficiency. The seamless integration of various components ensures streamlined operations and enhances workflow. A well-structured auto labor guide encompasses crucial elements such as labor cost calculation, time estimation methodologies, and integration with workshop management tools. Each component plays a distinctive role in contributing to the overall efficiency of the repair shop.
Labor Cost Calculation
Labor cost calculation is a pivotal aspect of the auto labor guide, as it encompasses various factors that impact cost estimation. Factors like technician skill level, complexity of the repair task, and overhead expenses significantly influence the final labor cost. Ensuring accurate labor cost calculation enables automotive repair shops to provide transparent pricing and fair quotes to customers. However, challenges may arise when adjusting for market variables such as fluctuating labor rates or supply chain disruptions. Adapting to these market variables while maintaining fair pricing practices is crucial for sustaining profitability and customer trust in the competitive automotive industry.
Time Estimation Methodologies
Time estimation methodologies within the auto labor guide involve the use of predictive algorithms, historical data analysis, and real-time monitoring. Predictive algorithms leverage machine learning to forecast labor times accurately based on specific repair tasks and technician performance. Utilizing historical data provides insights into past repair times, enabling shops to optimize scheduling and improve time efficiency. Real-time monitoring and updates allow for adjustments to be made on the fly, ensuring precision in time estimates and timely completion of repairs. Each methodology brings a unique advantage to the table, contributing to the overall effectiveness of the auto labor guide in optimizing efficiency.
Integration with Workshop Management Tools
Seamless integration with workshop management tools offers numerous benefits, including enhanced workflow coordination and automated billing processes. By integrating the auto labor guide with management software, repair shops can centralize data, streamline communication, and improve task allocation. Seamless integration also facilitates real-time updates on repair progress, ensuring technicians have access to the most current information. Enhanced workflow coordination minimizes errors, optimizes resource allocation, and ultimately increases operational efficiency. Moreover, automating billing processes eliminates manual errors, improves billing accuracy, and enhances customer satisfaction by providing transparent and consistent invoicing. The integration of workshop management tools with the auto labor guide is fundamental in modernizing repair shop operations and staying competitive in the automotive industry.
Implementation Strategies for Auto Labor Guides
In this segment, we delve into the critical aspect of Implementation Strategies for Auto Labor Guides within the context of optimizing efficiency in automotive repair shops. By focusing on specific elements such as staff training, monitoring, and adapting to industry trends, these strategies play a pivotal role in enhancing operational workflows and ensuring cost-effective services.
Training Staff on Efficiency
Educating Technicians on Guide Utilization
When it comes to Educating Technicians on Guide Utilization, the emphasis lies on empowering frontline staff with the necessary tools and knowledge to utilize the auto labor guide effectively. By familiarizing technicians with the guide's interface, time estimation methodologies, and integration with workshop management tools, repair shops can significantly enhance their service delivery.
Incorporating Best Practices Workshops

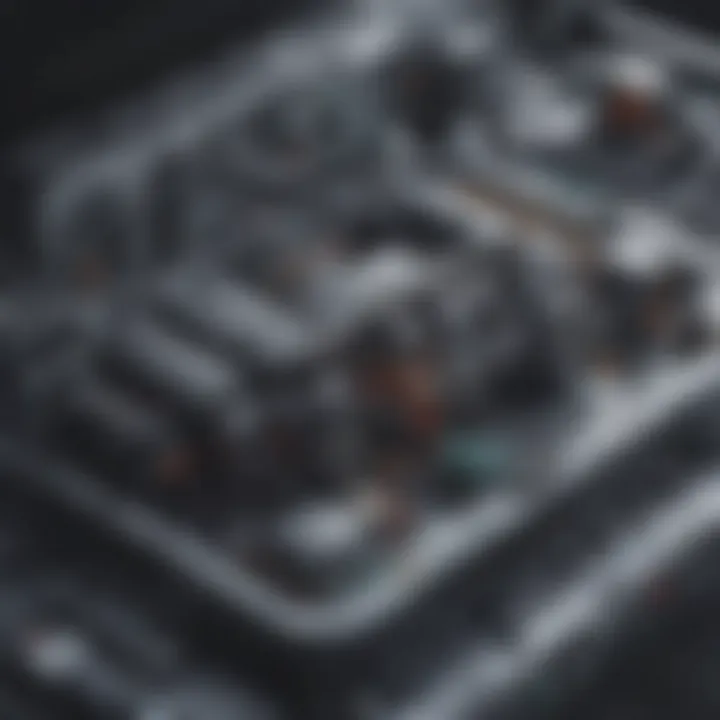
Incorporating Best Practices Workshops involves creating a structured learning environment where technicians can refine their skills, stay updated on industry trends, and exchange knowledge regarding optimal repair methodologies. These workshops provide a platform for technicians to collaborate, learn from each other's experiences, and implement industry best practices to improve overall repair shop efficiency.
Continuous Learning Culture
Maintaining a Continuous Learning Culture is paramount in sustaining operational excellence within automotive repair shops. By fostering a work environment that promotes ongoing training, skill development, and knowledge sharing, businesses can adapt to technological advancements, industry shifts, and customer demands effectively. This approach not only boosts staff morale and engagement but also positions repair shops as leaders in the rapidly evolving automotive landscape.
Monitoring and Evaluation
Establishing Performance Metrics
Establishing Performance Metrics involves defining key performance indicators (KPIs) to gauge the effectiveness of auto labor guide implementation. By measuring metrics such as turnaround time, accuracy of cost estimates, and customer satisfaction levels, repair shops can identify areas for improvement, optimize resource allocation, and enhance overall operational efficiency.
Regular Audits and Updates
Regular Audits and Updates are essential to ensuring the efficacy of auto labor guide utilization over time. By conducting routine audits of data accuracy, guide relevancy, and technician compliance, repair shops can proactively address any discrepancies, update labor guides as needed, and maintain a high standard of service delivery.
Feedback Loops for Improvement
Implementing Feedback Loops for Improvement involves creating mechanisms for technicians and customers to provide input on the auto labor guide's usability, accuracy, and relevance. By collecting feedback through surveys, focus groups, and direct interactions, repair shops can iteratively improve their labor guide processes, address pain points, and enhance overall service quality.
Adapting to Industry Trends
Industry Benchmarking
Industry Benchmarking entails comparing repair shop performance against industry standards and competitors to identify areas of strength and opportunities for growth. By analyzing industry trends, pricing strategies, and customer preferences, businesses can position themselves as market leaders, implement best practices, and drive continuous improvement.
Integrating Io
T and AI Technologies ####
Integrating Io T and AI Technologies involves leveraging cutting-edge technologies to streamline operational processes, enhance diagnostic accuracy, and optimize resource allocation. By integrating IoT sensors for real-time monitoring, AI algorithms for predictive maintenance, and automation tools for billing processes, repair shops can significantly boost efficiency, reduce manual errors, and deliver superior customer experiences.
Future-Proofing Strategies
Future-Proofing Strategies focus on adopting scalable, flexible solutions that can adapt to future industry changes and technological advancements. By investing in training programs for emerging technologies, establishing partnerships with tech providers, and embracing a culture of innovation, repair shops can future-proof their operations, stay ahead of the competition, and drive sustainable growth.
Benefits and ROI of Real-Time Auto Labor Guides
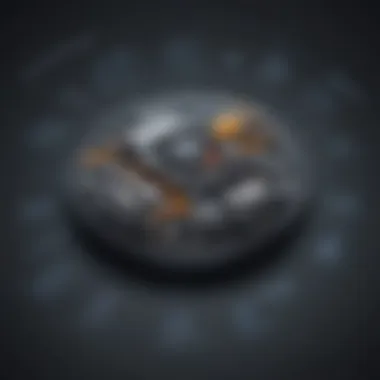
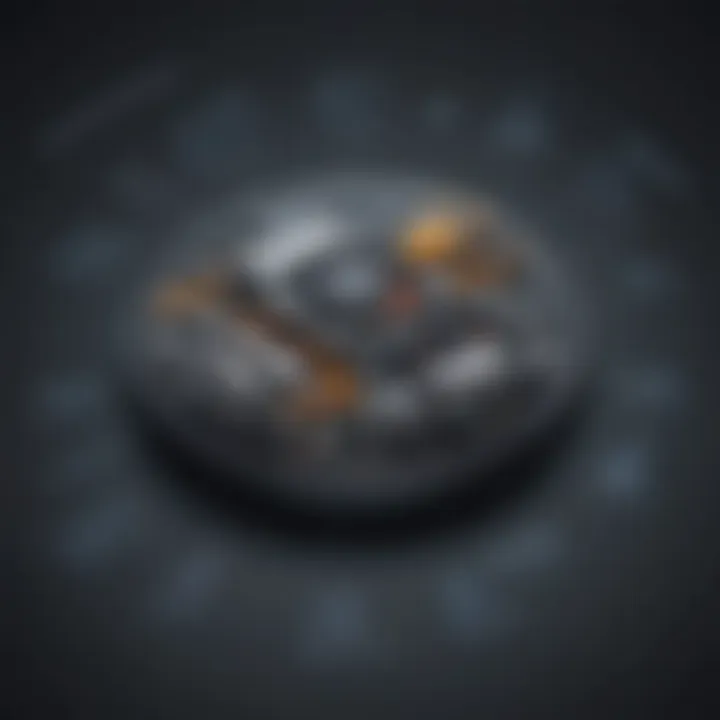
Real-Time Auto Labor Guides play a pivotal role in enhancing efficiency within automotive repair shops. By meticulously analyzing the Benefits and ROI of Real-Time Auto Labor Guides, we uncover how these guides drive operational excellence and financial success. Operational Efficiency is significantly boosted through Reduced Labor Costs, which involve meticulously calculating labor expenses to streamline operations and ensure optimum resource allocation. Improved Customer Service is another crucial aspect where the focus is on enhancing client satisfaction, fostering loyalty, and building a stellar reputation. Furthermore, Optimal Resource Allocation enables efficient utilization of resources, leading to enhanced productivity and cost-effectiveness.
Operational Efficiency
Reduced Labor Costs
Reduced Labor Costs are a cornerstone of operational success in automotive repair shops. By accurately estimating labor expenses and accounting for various factors affecting costs, such as wage rates and task complexity, businesses can optimize their budgeting and pricing strategies. This meticulous approach ensures that the workforce is efficiently utilized, tasks are completed within budget constraints, and profitability is maximized. However, a potential disadvantage of solely focusing on cost reduction is the risk of compromising on quality or cutting corners to minimize expenses, which could impact service quality and customer satisfaction.
Improved Customer Service
Enhancing Customer Service is paramount for automotive repair shops looking to establish long-term relationships with clients and differentiate themselves from competitors. By providing timely updates, transparent communication, and personalized assistance, shops can cultivate trust and loyalty among customers. The key advantage of prioritizing customer service is the potential for increased customer retention, positive reviews, and referrals, which are invaluable for sustaining business growth. Conversely, a challenge in delivering excellent customer service lies in balancing personalized care with operational efficiency, as excessive focus on one aspect may detract from the other.
Optimized Resource Allocation
Optimized Resource Allocation involves strategically managing human resources, equipment, and inventory to maximize efficiency and minimize waste. By identifying bottlenecks, reallocating staff based on skillsets and workload, and optimizing inventory levels, repair shops can streamline workflows and enhance productivity. The main advantage of resource optimization is the ability to reduce idle time, improve task prioritization, and boost overall operational output. However, challenges may arise in accurately forecasting demand, balancing workload distribution, and integrating new technologies seamlessly into existing processes.
Financial Impact
Increased Profit Margins
Increased Profit Margins are a direct result of operational efficiency and smart financial management. By closely monitoring costs, identifying cost-saving opportunities, and optimizing pricing strategies, repair shops can bolster their profitability and long-term sustainability. The primary benefit of increased profit margins is the financial stability it provides, enabling reinvestment in business growth, expansion, and innovation. Yet, a potential pitfall of solely focusing on profit margins is overlooking non-financial KPIs or sacrificing service quality for short-term financial gains.
Transparency in Billing
Transparency in Billing is crucial for fostering trust with customers and ensuring accountability in financial transactions. By providing detailed breakdowns of costs, explaining pricing methodologies, and addressing any discrepancies promptly, repair shops can enhance their credibility and reputation. The key advantage of transparent billing practices is the ability to build long-term relationships based on honesty, fairness, and integrity. However, challenges may arise in communicating complex pricing structures to customers effectively, managing expectations, and resolving billing disputes in a satisfactory manner.
Competitive Pricing Strategies
Developing Competitive Pricing Strategies is essential for navigating a dynamic market landscape and attracting price-conscious customers. By evaluating competitors' pricing, conducting cost analyses, and positioning their offerings effectively, repair shops can capture market share and drive customer acquisition. The primary benefit of competitive pricing is the potential for increased sales volume, market visibility, and sustainable revenue growth. Yet, a potential drawback of aggressive pricing strategies is the risk of engaging in price wars, eroding profit margins, and devaluing the brand in the long run.
Customer Satisfaction and Retention
Timely Service Delivery
Timely Service Delivery is a cornerstone of customer satisfaction, reflecting a repair shop's commitment to efficiency and professionalism. By adhering to promised timelines, minimizing wait times, and optimizing service processes, shops can meet and exceed customer expectations. The primary advantage of timely service delivery is the positive impact on customer loyalty, satisfaction levels, and brand reputation. However, challenges may arise in balancing speed with quality, managing unexpected delays, and maintaining consistent service standards across varied workloads.
Accurate Cost Estimates
Providing Accurate Cost Estimates is essential for building trust and transparency with customers, ensuring financial predictability, and avoiding billing disputes. By conducting thorough assessments, factoring in labor costs, parts pricing, and additional services upfront, repair shops can set clear expectations and eliminate surprises for clients. The key benefit of accurate cost estimates is establishing credibility, fostering customer trust, and enhancing overall service experiences. Nevertheless, challenges may surface in accurately predicting unforeseen expenses, managing customer expectations, and adapting estimates to changing market conditions.
Building Trust and Loyalty
Building Trust and Loyalty is a long-term investment that drives customer retention, referrals, and sustainable business growth. By prioritizing honest communication, delivering consistent quality service, and addressing customer concerns proactively, repair shops can establish strong relationships and positive brand associations. The main advantage of building trust and loyalty is the potential for brand advocacy, repeat business, and positive word-of-mouth marketing. However, challenges may arise in maintaining service quality standards, responding to feedback effectively, and ensuring seamless customer experiences throughout the service lifecycle.