Unleashing the Potential of Mold Flow Software for Advanced Product Design Optimization

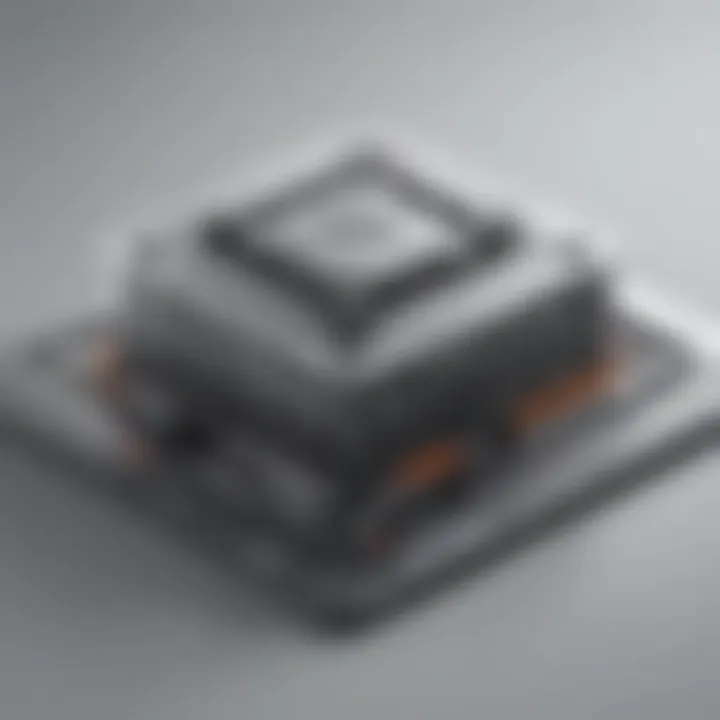
Software Overview As an expert in the realm of mold flow software for optimized product design, it is imperative to commence by navigating through the essentials of this advanced technological tool. Mold flow software serves as a crucial mechanism in the enhancement of product design processes. By scrutinizing the functions and advantages of mold flow software across a spectrum of industries, one can unearth the underlying principles that drive innovation and efficiency in product development endeavors. When dissecting the software, it is vital to consider facets like its introduction, key functionalities, as well as pricing plans and available subscription options. Investing time in comprehending these elements is fundamental towards harnessing the prowess of mold flow software for attaining superior product design outcomes.
User Experience Transitioning into the examination of user experience within the mold flow software domain, focusing on aspects that cater to ease of navigation and operational proficiency becomes paramount. Evaluating the user interface alongside navigational components offers insights into the ergonomic design of the software platform. Delving deeper into user experience involves unpacking details surrounding usability and the learning curve associated with engaging with mold flow software. Additionally, considerations for customer support provisions and their reliability factor heavily into the overall user experience equation. Ensuring that users are equipped with seamless interactions and accessible assistance consolidates the user experience within the realm of mold flow software implementation. ## formance and Reliability The performance and reliability of mold flow software play instrumental roles in determining its effectiveness within product design frameworks. Analyzing the efficiency and speed at which the software operates sheds light on its capacity to streamline design processes efficiently. Monitoring uptime and downtime statistics offers a glimpse into the software's stability and operational consistency. Exploring integration capabilities with other compatible tools underscores the software's adaptability within diverse technological ecosystems. By scrutinizing these performance and reliability metrics, discerning users can acutely gauge the impact of mold flow software on elevating product design outcomes. ## Se ty and Compliance Safeguarding data integrity and upholding compliance standards are cornerstones in the discourse surrounding mold flow software utilization. Delving into the encryption protocols and security measures employed by the software delineates its commitment to data protection practices. Assessing compliance with industry regulations underscores the software's adherence to pertinent legal frameworks governing data management practices. Furthermore, elucidating backup and disaster recovery protocols bolsters trust in the software's reliability during unforeseen contingencies. Embracing robust security and compliance measures within mold flow software implementation assures users of a fortified operational landscape conducive to unhindered product design innovation.
Introduction to Mold Flow Software
Mold flow software holds a critical role in enhancing product design processes across industries. By providing in-depth insights into mold behavior and material flow dynamics, this software empowers designers to optimize product quality and manufacturing efficiency. The ability to simulate various molding processes enables precise analysis of material behavior under different conditions, allowing businesses to make informed decisions at every stage of product development. The significance of mold flow software lies in its capacity to minimize defects, ensure optimal material distribution, and accelerate design iterations, ultimately leading to cost savings and improved time efficiency.
Understanding Mold Flow Analysis
Theoretical Basis of Mold Flow Analysis
One fundamental aspect of mold flow analysis is its theoretical underpinnings, which drive the predictive capabilities of the software. By utilizing complex algorithms and mathematical models, mold flow software can simulate material flow with a high degree of accuracy. This theoretical foundation enables designers to forecast potential issues in the molding process, leading to proactive problem-solving and efficient design optimization. The unique feature of theoretical mold flow analysis lies in its ability to provide detailed insights into flow patterns, pressure distribution, and cooling behavior, facilitating informed decision-making for product enhancement.
Importance of Mold Flow Simulation in Product Development
The importance of mold flow simulation in product development cannot be overstated. It plays a pivotal role in identifying manufacturing challenges early on, allowing for adjustments to be made before the production phase. By simulating the molding process, designers can visualize material behavior, detect potential defects, and optimize mold designs for enhanced product quality. Mold flow simulation acts as a virtual testing ground, mitigating risks associated with tooling issues and ensuring that the final product meets or exceeds quality standards. Its unique feature lies in its ability to validate designs efficiently, reducing costly errors and maximizing process efficiency.
Evolution of Mold Flow Software
Technological Advancements in Mold Flow Tools
The evolution of mold flow software has been propelled by significant technological advancements, enhancing its simulation capabilities and user interface. Modern tools leverage advanced algorithms and computations to deliver precise simulations for a wide range of molding processes. These advancements have streamlined the design iteration process, enabling faster prototyping and validation of complex molds. The key characteristic of these technological advancements lies in their ability to offer real-time feedback, improving decision-making processes and overall product design outcomes.
Impact of Digitalization on Mold Flow Solutions
Digitalization has revolutionized mold flow solutions by facilitating seamless integration with other digital technologies. From IoT connectivity for real-time monitoring to AI-powered predictive analytics, digitalization has expanded the functionalities of mold flow software, making it indispensable in the era of Industry 4.0. The key characteristic of this impact is its ability to enable data-driven decision-making, optimize production processes, and enhance collaboration among design teams. By harnessing digitalization, businesses can achieve greater efficiency, precision, and innovation in their product design endeavors.
Key Features of Mold Flow Software
Simulation Capabilities for Different Molding Processes
One of the key features of mold flow software is its diverse simulation capabilities across various molding processes. Whether it's injection molding, blow molding, or extrusion, the software can simulate each process with accuracy and detail. This versatility allows designers to tailor simulations to specific manufacturing requirements, optimizing material choice, mold design, and production parameters. The unique feature of simulation capabilities lies in their ability to provide comprehensive insights into the entire molding process, from material flow and cooling to warp analysis and shrinkage prediction.
Analysis of Material Behavior under Varying Conditions
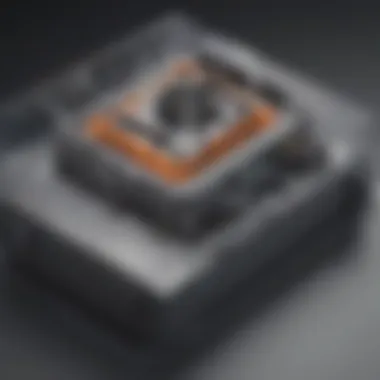
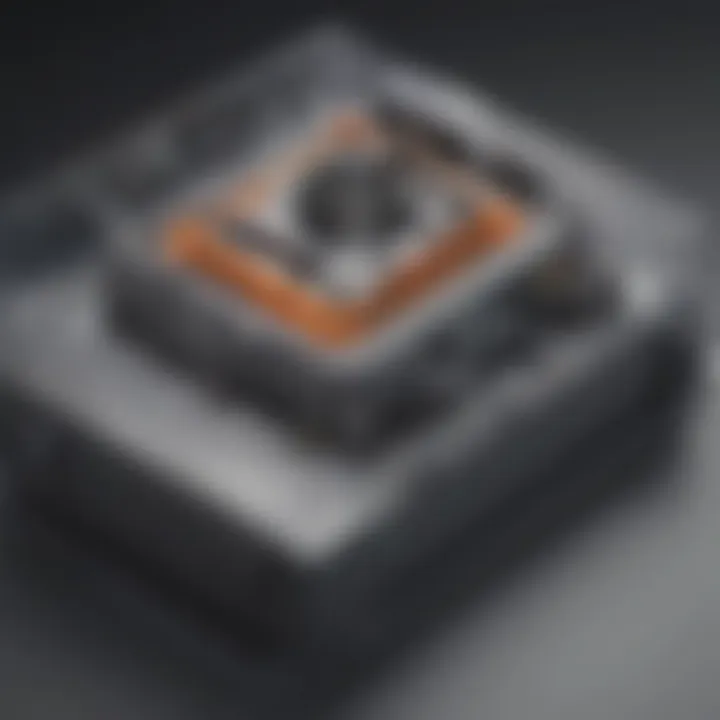
Another essential feature of mold flow software is its ability to analyze material behavior under different conditions. By simulating varying temperatures, pressures, and flow rates, the software can predict how materials will behave during the molding process. This analysis is crucial for ensuring product quality, as it helps designers anticipate issues such as warping, sink marks, or incomplete filling. The unique feature of material behavior analysis lies in its predictive nature, enabling designers to preemptively address potential defects and refine product designs for optimal performance.
Applications Across Industries
Mold flow software holds significant importance in various industries, revolutionizing product design processes. Its utilization across different sectors like automotive, consumer goods, and medical devices brings about substantial benefits and advancements. By integrating mold flow software into the design workflow, industries can enhance efficiency, accuracy, and quality while minimizing costs and time investments. The adaptability of this software across different manufacturing processes and materials enables businesses to tailor their product development strategies with precision and foresight.
Automotive Sector
Enhancing Vehicle Component Design
Enhancing vehicle component design is a crucial aspect in the automotive sector, contributing to overall operational excellence and product performance. This specific feature of mold flow software allows engineers to simulate and optimize the design of vehicle parts, ensuring structural integrity, durability, and functionality. The ability to analyze material behavior and predict performance under varying conditions makes it a valuable tool for crafting innovative and reliable automotive components. Despite its complexity, this aspect of mold flow software presents a streamlined solution for fine-tuning designs and achieving optimal results in the competitive automotive market.
Improving Manufacturing Efficiency
Enhancing manufacturing efficiency through mold flow software implementation is paramount for reducing production costs and enhancing output quality. This facet focuses on streamlining the manufacturing process, identifying potential bottlenecks, and optimizing the overall production line. By utilizing simulations and predictive analytics, manufacturers can fine-tune their operations, minimize defects, and expedite time-to-market for new vehicle models. Although challenges such as data accuracy and system integration may arise, the overall benefits of efficiency improvement overshadow any initial obstacles, making it a strategic choice for the automotive industry.
Consumer Goods
Optimizing Packaging Solutions
Optimizing packaging solutions using mold flow software is a game-changer for consumer goods companies looking to enhance product presentation and protection. This feature enables designers to simulate various packaging designs, materials, and configurations to achieve optimal results. By considering factors like material distribution, packaging strength, and visual appeal, businesses can create packaging solutions that are not only aesthetically pleasing but also functional and cost-effective. Despite the need for comprehensive data input and iterative testing, the ability to refine packaging designs accurately through simulation makes this aspect of mold flow software indispensable for consumer goods manufacturers.
Ensuring Product Durability
Ensuring product durability through mold flow software analysis is critical for maintaining product quality and customer satisfaction in the consumer goods industry. This functionality allows manufacturers to simulate the performance of products under different conditions, predict potential weak points, and optimize material usage for longevity. By pinpointing areas of improvement and validating durability early in the design phase, companies can mitigate risks of product failure, warranty claims, and recalls. Although the initial set-up and calibration may require time and resources, the long-term benefits of producing durable and reliable consumer goods justify the investment in this capability.
Medical Devices
Ensuring Precision in Device Manufacturing
The precision in device manufacturing facilitated by mold flow software is a cornerstone for the medical devices sector, where accuracy and reliability are paramount. This feature empowers manufacturers to simulate intricate device geometries, material interactions, and manufacturing processes with exceptional precision. By predicting how different factors impact device performance and quality, engineers can optimize designs for functionality, sterilization, and regulatory compliance. Despite the challenge of modeling complex medical devices and validating simulations against real-world outcomes, the meticulous approach enabled by this aspect of mold flow software is invaluable for ensuring the safety and efficacy of medical devices.
Validating Sterilization Processes
Validating sterilization processes using mold flow software is a critical step in ensuring the efficacy and safety of medical devices in healthcare settings. This function allows regulatory bodies and manufacturers to model sterilization methods, assess material compatibility, and verify microbial eradication. By simulating sterilization conditions and analyzing the effects on device materials and structures, stakeholders can proactively address potential contamination risks and compliance issues. While the intricacies of sterilization simulation and data interpretation pose challenges, the capability to validate sterilization processes using mold flow software enhances the overall quality control measures and regulatory adherence for medical device manufacturers.
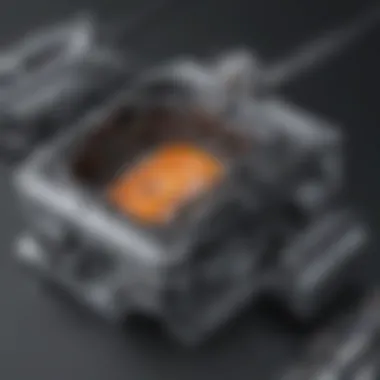
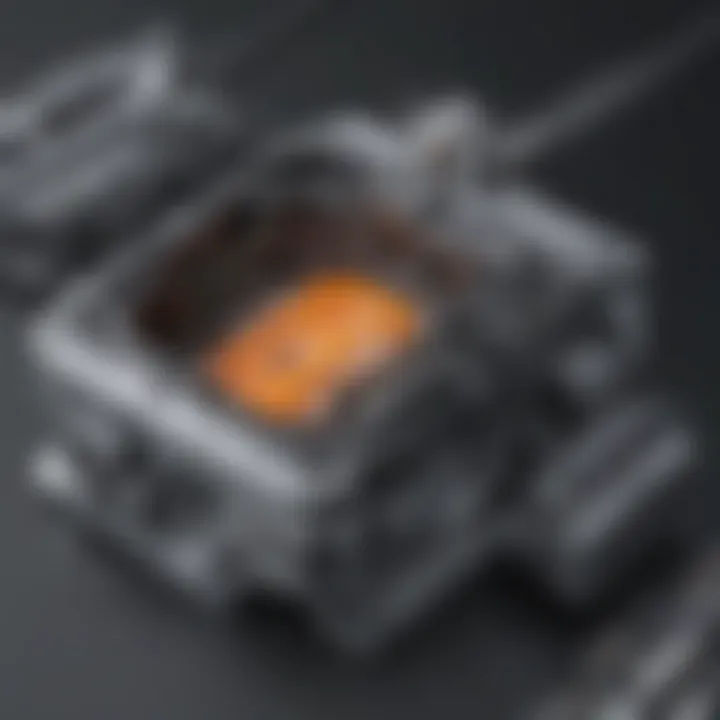
Benefits of Implementing Mold Flow Software
Motivating the integration of mold flow software is the imperative objective of enhancing product design. In the realm of product development, the deployment of mold flow software presents a myriad of advantages, shaping the landscape of innovation and efficiency. By delving into the intricacies of this technology, businesses can unlock new possibilities for streamlining design processes and optimizing manufacturing outcomes.
Cost Savings and Time Efficiency
Embarking on the journey of cost savings and time efficiency through the implementation of mold flow software heralds a paradigm shift in product development strategies. Unveiling the essence of this shift involves a meticulous examination of the pivotal aspects that embody the reduction of prototyping costs and accelerated design iterations.
Reduction of Prototyping Costs
Central to the discourse of cost optimization is the reduction of prototyping expenses, a cornerstone in achieving economical design iterations. This facet of mold flow software empowers manufacturers to minimize the financial overhead associated with traditional prototyping methods, consequently streamlining the product development lifecycle. Innovation is propelled by the affordability and accessibility offered by this feature, enabling businesses to allocate resources more judiciously and foster a culture of continuous improvement.
Accelerated Design Iterations
The impetus for rapid innovation lies within the realm of accelerated design iterations facilitated by mold flow software. This dynamic functionality expedites the product development timeline, fostering a responsive environment for iterative design enhancements. Drawing from real-time simulation feedback, designers and engineers can iterate swiftly, refining product attributes and performance metrics with precision. This agile approach to design iteration not only expedites time-to-market but also cultivates a culture of innovation and adaptability within organizations.
Enhanced Product Quality
Elevating product quality standards is the crux of operational excellence enabled by mold flow software. By addressing critical aspects such as minimized defects and flaws along with optimized material distribution, businesses can fortify their competitive edge and ensure customer satisfaction.
Minimized Defects and Flaws
Ensuring product integrity is synonymous with the elimination of defects and flaws, a cornerstone in enhancing consumer confidence and loyalty. Mold flow software empowers manufacturers to mitigate quality issues by pinpointing potential flaws and irregularities in the design phase itself. This proactive approach not only averts costly recalls and rework but also cements a reputation for quality and reliability in the market.
Optimized Material Distribution
Harnessing the power of optimized material distribution is imperative in enhancing product performance and durability. Mold flow software equips designers with the tools to analyze material behavior under varying conditions, enabling them to optimize material distribution for superior product functionality. This emphasis on material efficiency not only enhances product durability but also minimizes material wastage, aligning with sustainable manufacturing practices.
Risk Mitigation and Design Validation
Mitigating risks and validating design decisions form the bedrock of design excellence, a realm where mold flow software shines. By offering insights into early issue identification and robust mold design validation, this software empowers businesses to navigate design challenges with confidence and precision.
Identification of Potential Issues Early On
Anticipating and addressing potential design pitfalls early on is paramount in fortifying product development outcomes. Mold flow software facilitates early issue identification by simulating design scenarios and highlighting critical areas of improvement. This preemptive approach enables designers to address vulnerabilities proactively, thereby reducing the likelihood of costly design revisions and delays.
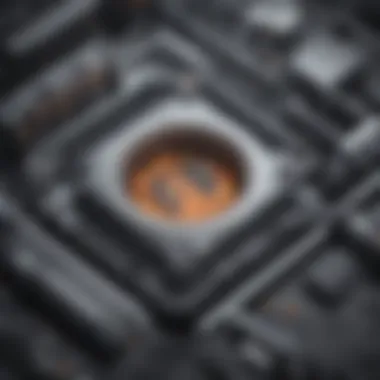
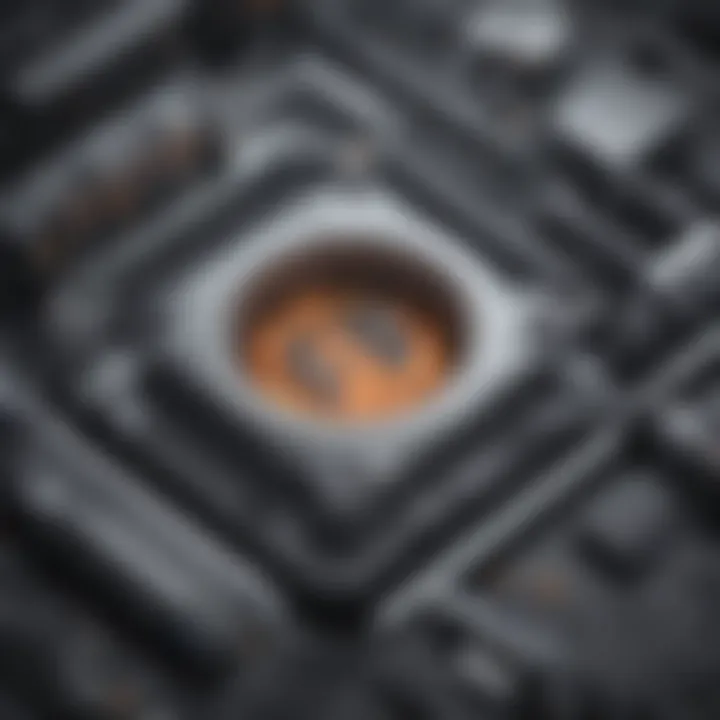
Validation of Mold Designs
Validating mold designs is a strategic imperative in ensuring manufacturing efficiency and product quality. Mold flow software functions as a virtual testing ground, enabling designers to validate mold designs through comprehensive simulations. By assessing factors like material flow, cooling rates, and part quality, businesses can fine-tune mold designs with precision, minimizing production delays and optimizing molding processes for superior outcomes.
Future Trends in Mold Flow Software
In this article, it is crucial to delve into the future trends shaping the landscape of mold flow software. The advancements in this technology are revolutionizing product design processes across industries. With a keen focus on integrating mold flow software with Industry 4.0 technologies, businesses can harness several benefits like improved efficiency and innovation. These trends pave the way for smarter, more automated design processes that can adapt to dynamic market demands.
Integration with Industry Technologies
AI-Powered Predictive Analytics
The integration of AI-powered predictive analytics into mold flow software holds immense significance in optimizing product design. This cutting-edge technology enables accurate forecasting of mold behavior, streamlining the design process by providing valuable insights for proactive decision-making. Its key characteristic lies in the ability to predict potential issues and optimize designs to enhance product quality efficiently. Despite its computational intensity, AI-powered predictive analytics proves to be a valuable and popular choice for companies seeking to improve their molding processes.
IoT Connectivity for Real-Time Monitoring
IoT connectivity for real-time monitoring offers real-time insights into mold flow parameters, enhancing overall operational efficiency. The ability to remotely monitor and adjust molding processes in real-time is a game-changer for manufacturers, enabling them to make timely interventions and prevent costly errors. The unique feature of IoT connectivity lies in its seamless data transmission, enabling continuous monitoring without physical presence. While it ensures operational transparency, it may pose security challenges that need to be addressed for seamless integration.
Advancements in Material Science
The advancements in material science are influencing mold flow simulations, particularly through biodegradable materials simulation and nanotechnology applications. These developments allow for more sustainable and innovative product designs, aligning with the growing demand for eco-friendly solutions. The key characteristic of biodegradable materials simulation lies in its ability to predict material behavior accurately under varying conditions, enabling designers to make informed decisions for environmentally-conscious products. Similarly, nanotechnology applications in mold flow provide unprecedented control over material properties, opening doors for novel design possibilities and enhanced product performance.
Biodegradable Materials Simulation
The integration of biodegradable materials simulation enhances the sustainability of product designs by offering insights into material behavior and degradation over time. This feature is beneficial for companies looking to reduce their environmental footprint and meet consumer demands for eco-friendly products. The unique advantage of biodegradable materials simulation lies in its predictive accuracy, allowing designers to simulate long-term effects of material choices in a controlled environment. However, challenges such as limited material databases may hinder its full potential in comprehensive design scenarios.
Nanotechnology Applications in Mold Flow
Nanotechnology applications in mold flow unlock the potential for material miniaturization and performance enhancement, broadening design possibilities for various industries. The key characteristic of nanotechnology lies in its ability to manipulate material structures at the nanoscale, offering unprecedented control over material properties and performance. This technology is a popular choice for manufacturers aiming to push the boundaries of traditional materials and explore new frontiers in product innovation. Despite its benefits, challenges related to scalability and cost-effective implementation may impact widespread adoption.
Customization and User-Friendly Interfaces
Tailored solutions for diverse industries and intuitive design for enhanced user experience are paramount in ensuring widespread adoption and usability of mold flow software. These features cater to the specific needs of different sectors and enhance user engagement, promoting a seamless design experience that drives efficiency and productivity.
Tailored Solutions for Diverse Industries
Tailored solutions for diverse industries offer customized functionalities that cater to the unique requirements of different sectors, ensuring optimal performance and scalability. The key characteristic of tailored solutions lies in their adaptability to industry-specific challenges, providing tailored insights and recommendations for efficient design processes. This tailored approach is a beneficial choice for businesses seeking tailored solutions that align with their specific production needs. However, ensuring compatibility with existing systems and workflows may pose integration challenges that need to be addressed.
Intuitive Design for Enhanced User Experience
Intuitive design for enhanced user experience focuses on simplifying the user interface and interaction design to streamline the mold flow software usage. This emphasis on user-friendly interfaces enhances user adoption and efficiency by reducing learning curves and minimizing errors. The unique feature of intuitive design lies in its ability to provide a seamless and enjoyable user experience, driving user engagement and satisfaction. While it enhances overall usability, balancing simplicity with advanced functionalities can be a delicate challenge that requires continuous user feedback and iterative improvements.
This in-depth exploration of future trends in mold flow software underscores the evolving landscape of product design processes and the pivotal role of innovative technologies in driving efficiency and innovation. By aligning with these trends, businesses can stay ahead of the curve and unlock new possibilities for optimized product development.