Maximo Maintenance System: A Comprehensive Guide for Optimal Asset Management
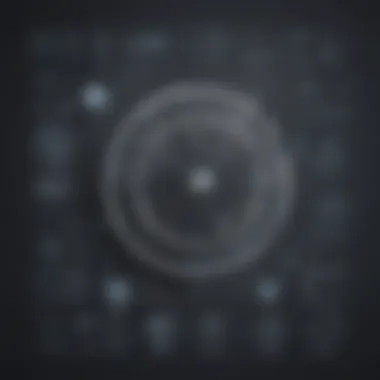
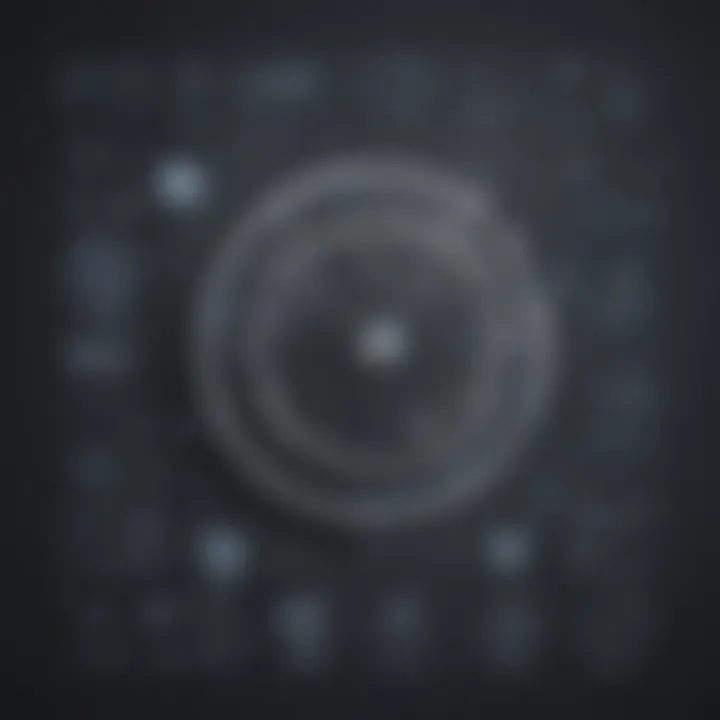
Software Overview
The Maximo Maintenance System is a comprehensive software solution designed for optimal asset management in businesses. It offers a range of key features and functionalities that streamline maintenance operations. Additionally, the software comes with various pricing plans and subscription options suitable for small to medium-sized businesses.
User Experience
When it comes to user experience, the Maximo Maintenance System prides itself on its intuitive user interface and seamless navigational elements. Users can easily navigate through the system, minimizing the learning curve for new adopters. Furthermore, the software provides reliable customer support options ensuring a smooth user experience.
Performance and Reliability
The Maximo Maintenance System excels in performance, offering speed and efficiency in managing maintenance tasks. The software boasts impressive uptime statistics, minimizing downtime for continuous operations. Moreover, its integration capabilities with other tools enhance overall performance and enable seamless workflow management.
Security and Compliance
In terms of security, the Maximo Maintenance System prioritizes data encryption and stringent security protocols to safeguard sensitive information. The software also complies with industry regulations, ensuring data protection and privacy for users. Additionally, robust backup and disaster recovery measures are in place to mitigate any potential risks or data loss incidents.
Introduction
In the vast landscape of asset management solutions, understanding the core principles of the Maximo Maintenance System becomes pivotal for businesses aiming to orchestrate optimal asset management strategies. This sect entails delving deep into the complexities of the Maximo Maintenance System, elucidating its key functionalities, and providing insights into leveraging this system for astute asset preservation and management. By scrutinizing the intricate layers of the Maximo Maintenance System, businesses can uncover a realm of possibilities that pave the path towards enhanced operational efficiency and streamlined asset upkeep.
Overview of Maximo Maintenance System
Key Features:
The Maximo Maintenance System encapsulates a plethora of essential features that collectively redefine traditional asset management norms. Its user-friendly interface and comprehensive functionality distinguish it as a frontrunner in the realm of asset management solutions. By meticulously organizing work orders, preventive maintenance schedules, and inventory control, Maximo ensures a holistic approach towards asset maintenance. The system's adaptability to varying business needs and seamless integration with existing infrastructures position it as a commendable choice for small to medium-sized businesses seeking an efficient asset management solution.
Benefits of Implementation:
Implementing the Maximo Maintenance System brings forth a myriad of benefits that augment the overall asset management landscape. From heightened operational efficiency to cost savings through preventive maintenance scheduling, the benefits of implementing Maximo are multifaceted. The system's automated notifications and streamlined work order management processes ensure that businesses can seamlessly navigate the complexities of asset maintenance. While the system may pose a learning curve during the initial phases, its long-term advantages overshadow any temporary impediments, making it a strategic investment choice.
Significance of Asset Management
Role in Business Efficiency:
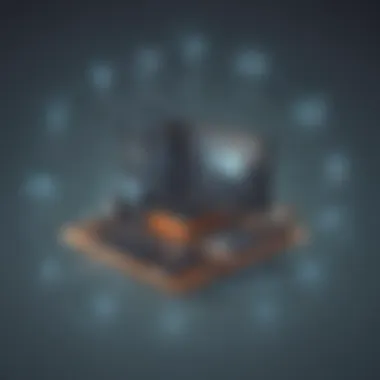
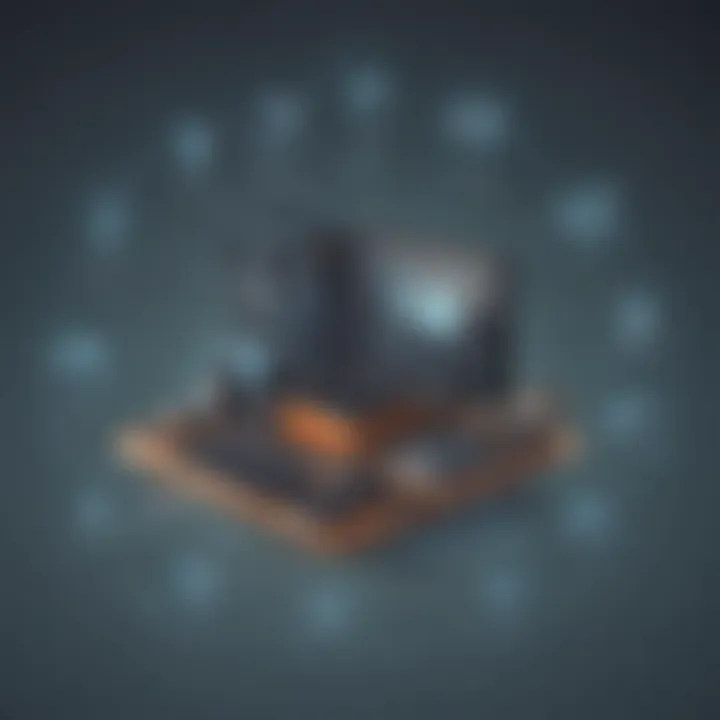
The role of asset management in bolstering business efficiency cannot be overstated. Efficient asset management streamlines operational processes, minimizes downtime, and optimizes resource allocation. Maximo Maintenance System plays a pivotal role in enhancing business productivity by offering a centralized platform for work order management and preventive maintenance scheduling. By leveraging Maximo's user-centric design and robust features, businesses can navigate the intricacies of asset management with precision.
Impact on Financial Performance:
The impact of robust asset management practices resonates profoundly in a business's financial performance. Effective asset management via systems like Maximo translates into improved cost controls, reduced maintenance expenses, and increased asset longevity. By ensuring that assets operate at optimal efficiency levels, businesses can mitigate unnecessary expenditures and bolster overall financial performance. Maximo's emphasis on data-driven decision-making further amplifies its impact on financial outcomes, making it an indispensable tool for businesses aiming to achieve fiscal stability through streamlined asset management strategies.
Key Functionalities
The Maximo Maintenance System offers a range of key functionalities essential for optimal asset management. These functionalities play a crucial role in streamlining maintenance operations, ensuring efficiency, and maximizing asset performance. From work order management to preventive maintenance scheduling and inventory control, each functionality serves a specific purpose in enhancing overall maintenance processes and asset longevity. By effectively utilizing these key functionalities, businesses can achieve cost savings, improve resource allocation, and minimize downtime, thereby boosting operational effectiveness and ensuring optimal asset performance.
Work Order Management
Creating Work Orders
Creating work orders is a fundamental aspect of work order management within the Maximo Maintenance System. It involves the initiation of maintenance tasks, detailing the necessary activities, and assigning responsibilities to relevant personnel. The creation of work orders facilitates a structured approach to maintenance activities, ensuring clarity, accountability, and timely execution of tasks. This feature enables users to prioritize maintenance tasks based on criticality, assign resources efficiently, and track progress effectively. The systematic creation of work orders enhances workflow management, promotes proactive maintenance practices, and ultimately contributes to prolonging asset lifespan and minimizing operational disruptions.
Prioritizing Tasks
In the realm of work order management, prioritizing tasks is a pivotal functionality that dictates the sequence and urgency of maintenance activities. By prioritizing tasks effectively, businesses can optimize resource allocation, minimize downtime, and address high-priority issues promptly. This feature allows users to categorize maintenance tasks based on criticality, safety requirements, and operational impact, enabling them to allocate resources judiciously and focus on tasks that directly impact asset performance. Prioritizing tasks enhances efficiency in task execution, reduces response times to critical issues, and ensures that maintenance efforts are aligned with organizational priorities, leading to enhanced asset reliability and operational efficiency.
Preventive Maintenance Scheduling
Setting Maintenance Schedules
Setting maintenance schedules is a crucial aspect of preventive maintenance within the Maximo Maintenance System. It involves defining recurring maintenance activities, establishing inspection intervals, and scheduling maintenance tasks in advance. By setting maintenance schedules, organizations can proactively address potential equipment failures, mitigate risks, and extend asset lifespan. This feature enables users to create preventive maintenance plans based on historical data, equipment specifications, and regulatory requirements, ensuring systematic adherence to maintenance schedules. Setting maintenance schedules helps in avoiding unplanned downtime, optimizing asset performance, and reducing maintenance costs, ultimately enhancing operational efficiency and asset reliability.
Automated Notifications
Automated notifications play a key role in preventive maintenance scheduling, providing real-time alerts and reminders for upcoming maintenance tasks and inspections. This functionality ensures that responsible personnel are promptly informed about scheduled maintenance activities, equipment servicing requirements, and compliance deadlines. Automated notifications help in mitigating missed maintenance events, improving maintenance planning, and enhancing overall maintenance compliance. By automating the notification process, businesses can streamline communication, increase operational transparency, and facilitate timely responses to maintenance alerts, thereby promoting proactive maintenance practices and optimizing asset performance.
Inventory Control
Managing Stock Levels
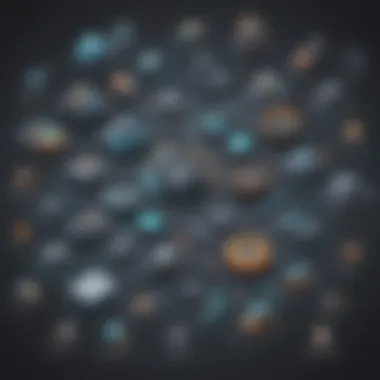
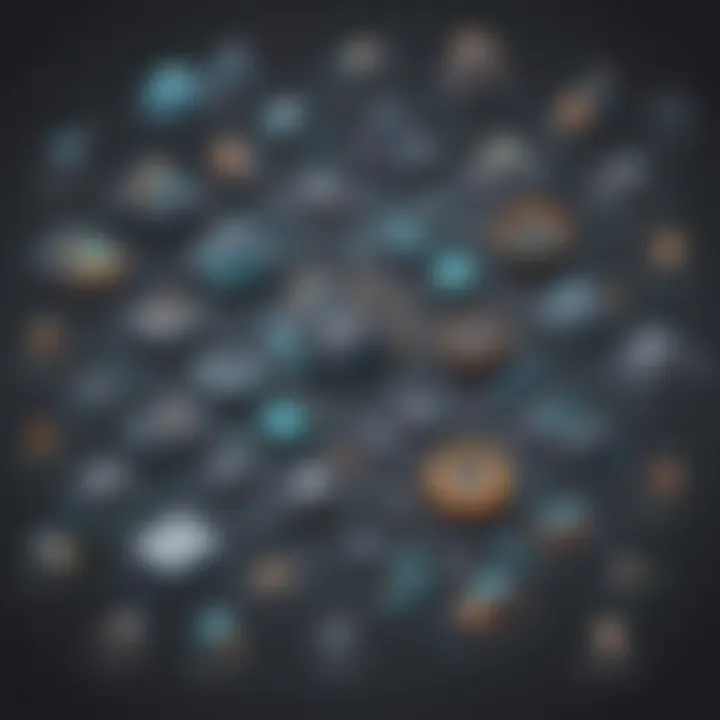
Effective inventory control is essential in optimizing asset management within the Maximo Maintenance System. Managing stock levels involves monitoring inventory quantities, tracking consumption rates, and ensuring adequate stock availability for maintenance activities. This functionality enables organizations to prevent stockouts, reduce excess inventory, and optimize inventory turnover, improving overall inventory management efficiency. By managing stock levels efficiently, businesses can minimize operational disruptions, lower carrying costs, and enhance inventory visibility, ultimately leading to improved maintenance operations and streamlined asset management.
Ordering Supplies
Ordering supplies is a critical aspect of inventory control, allowing businesses to replenish stock, procure necessary parts, and maintain optimal inventory levels. This functionality facilitates the seamless ordering of supplies based on predefined thresholds, demand forecasts, and consumption patterns, ensuring timely availability of required materials for maintenance tasks. By simplifying the supply procurement process, ordering supplies helps in reducing lead times, minimizing stock shortages, and optimizing inventory costs. This feature enhances operational readiness, supports timely maintenance activities, and contributes to overall efficiency in asset management within the Maximo Maintenance System.
Implementation Strategies
In this section, we delve into the critical area of Implementation Strategies. Understanding and effectively implementing strategies in the context of asset management can significantly impact business operations. By focusing on specific elements such as planning, execution, and evaluation, businesses can enhance efficiency and productivity. Implementation Strategies play a crucial role in ensuring the successful integration of the Maximo Maintenance System within an organization. Businesses need to consider factors like alignment with organizational goals, resource allocation, and timeline management to streamline the implementation process.
Planning and Preparation
Assessing Organizational Needs
Assessing Organizational Needs is a fundamental aspect of the Implementation Strategies. By conducting a thorough evaluation of the current state of the organization, including existing maintenance practices and systems, businesses can identify gaps and determine the requirements for implementing the Maximo Maintenance System. This process involves analyzing maintenance workflows, identifying key stakeholders, and assessing the readiness of the organization for change. The key characteristic of Assessing Organizational Needs lies in its ability to provide insights into specific areas that require improvement, thus enabling tailored solutions to be developed.
Defining Implementation Goals
Defining Implementation Goals is paramount in ensuring a clear direction for the implementation of the Maximo Maintenance System. By defining specific and measurable goals related to asset management, organizations can establish a roadmap for success. This process involves setting achievable targets, outlining milestones, and aligning implementation goals with overarching business objectives. The unique feature of Defining Implementation Goals is its ability to provide a framework for tracking progress and measuring the success of the implementation process, helping organizations stay focused and on track.
Training and Integration
User Training Programs
User Training Programs are essential for the successful adoption of the Maximo Maintenance System. Providing comprehensive training programs to users ensures that they have the necessary skills and knowledge to effectively utilize the system. The key characteristic of User Training Programs is their focus on enhancing user proficiency, promoting system awareness, and empowering users to maximize the system's capabilities. By investing in user training, organizations can minimize downtime, reduce errors, and optimize the use of the Maximo Maintenance System within their operations.
Integration with Existing Systems
Integration with Existing Systems is a critical aspect of implementing the Maximo Maintenance System seamlessly. By integrating the system with existing software and technologies used within the organization, businesses can enhance data accuracy, improve workflow efficiency, and leverage existing infrastructure. The key characteristic of Integration with Existing Systems lies in its ability to facilitate data exchange between systems, streamline processes, and ensure compatibility across platforms. Organizations can benefit from cost savings, enhanced data visibility, and improved decision-making by effectively integrating the Maximo Maintenance System with their existing systems.
Monitoring and Evaluation
Tracking Performance Metrics
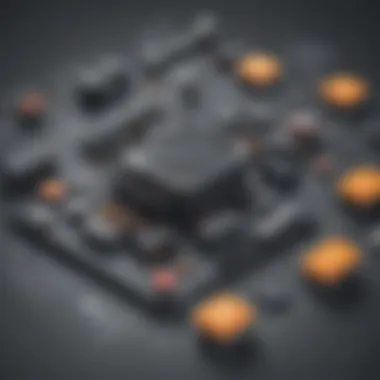
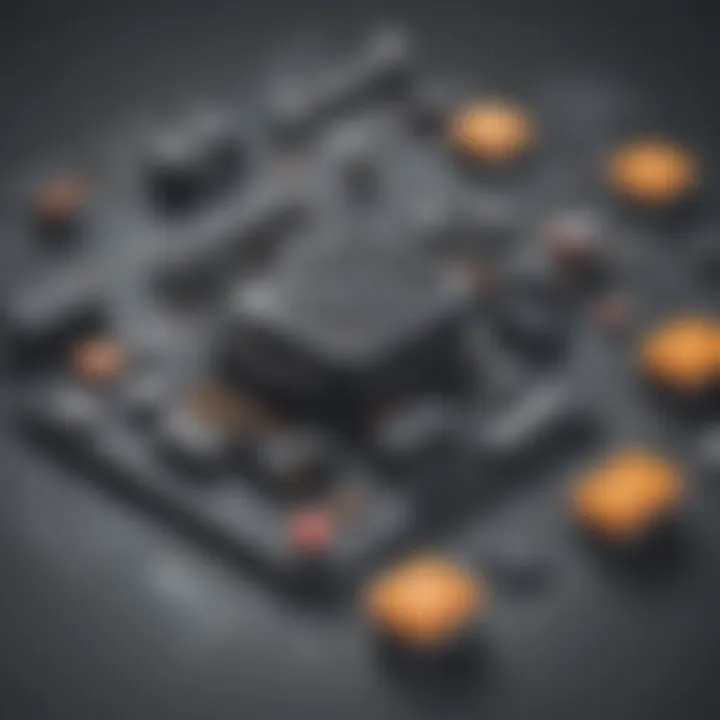
Tracking Performance Metrics is vital for assessing the effectiveness of the Maximo Maintenance System implementation. By establishing key performance indicators (KPIs) and metrics, organizations can measure the impact of the system on maintenance operations and overall asset management. The key characteristic of Tracking Performance Metrics is its ability to provide quantifiable data on system performance, workflow efficiency, and maintenance outcomes. By tracking performance metrics, organizations can identify areas for improvement, optimize processes, and drive continuous enhancement of maintenance practices.
Feedback and Iterative Improvements
Feedback and Iterative Improvements are essential components of the monitoring and evaluation process. By gathering feedback from users, stakeholders, and maintenance teams, organizations can gain valuable insights into system usability, functionality, and impact on daily operations. The key characteristic of Feedback and Iterative Improvements is their role in fostering a culture of continuous improvement within the organization. By incorporating feedback into system enhancements and making iterative improvements based on user input, organizations can enhance user satisfaction, system performance, and overall asset management effectiveness.
Best Practices
In this section, we delve into the critical aspects of best practices related to the Maximo Maintenance System. The implementation of best practices holds paramount importance in ensuring the optimal functioning of the system. By adhering to established guidelines and industry standards, businesses can enhance their asset management efficiency. Best practices encompass a wide range of strategies, methodologies, and protocols that are proven to deliver superior results in maintenance operations. Implementing best practices not only improves overall performance but also minimizes risks and maximizes the longevity of assets.
Data Analysis and Reporting
Utilizing Analytical Tools
Discussing the utilization of analytical tools within the context of the Maximo Maintenance System is crucial for gaining actionable insights from the data collected. Analytical tools aid in processing vast amounts of information to identify trends, anomalies, and optimization opportunities. They play a pivotal role in decision-making processes by providing comprehensive data visualization and predictive analytics capabilities. The unique feature of analytical tools lies in their ability to transform raw data into meaningful metrics, facilitating data-driven decision-making. While advantageous in enhancing operational efficiency, analytical tools require initial investment and continuous training for proficient utilization.
Generating Custom Reports
The generation of custom reports is instrumental in producing tailored insights specific to the organization's requirements. Custom reports allow for the visualization of key performance indicators, maintenance trends, and financial metrics in a personalized format. They offer flexibility in data presentation, enabling stakeholders to focus on pertinent information for strategic decision-making. Custom reports provide a detailed snapshot of asset performance, work order status, and resource utilization, aiding in the identification of inefficiencies and areas for improvement. Despite their benefits in facilitating targeted analysis, generating custom reports necessitates expertise in report building and a comprehensive understanding of data mapping.
Optimizing Maintenance Processes
Streamlining Workflows
Efficient streamlining of workflows is essential for maximizing the effectiveness of maintenance processes within the Maximo Maintenance System. Streamlined workflows eliminate redundancies, reduce response times, and enhance overall operational productivity. The key characteristic of streamlined workflows lies in their ability to simplify complex tasks, minimize bottlenecks, and allocate resources optimally. By streamlining workflows, organizations can achieve cost savings, improved service delivery, and heightened service quality. However, implementing streamlined workflows requires thorough process mapping, stakeholder collaboration, and continuous monitoring for sustained efficiency gains.
Integrating IoT Technologies
The integration of Internet of Things (IoT) technologies presents a valuable opportunity to revolutionize maintenance processes within the Maximo Maintenance System. IoT technologies enable connected devices to transmit real-time data, enabling predictive maintenance, remote monitoring, and asset tracking. The key characteristic of IoT integration is its ability to enhance asset visibility, automate data collection, and bolster predictive maintenance capabilities. By integrating IoT technologies, organizations can proactively address maintenance issues, reduce downtime, and extend asset lifespan. Nevertheless, integrating IoT technologies mandates robust cybersecurity measures, data privacy protocols, and ongoing maintenance of connected devices.
Continuous Improvement Culture
Encouraging Employee Feedback
Fostering a culture that encourages employee feedback is indispensable for driving continuous improvement within the framework of the Maximo Maintenance System. Employee feedback serves as a valuable source of insights into operational challenges, user experiences, and process inefficiencies. The key characteristic of encouraging employee feedback lies in promoting open communication, constructive criticism, and proactive problem-solving. By valuing employee perspectives, organizations can uncover innovative solutions, boost employee engagement, and foster a culture of continuous learning. Despite its benefits in promoting organizational growth, encouraging employee feedback requires receptive leadership, transparent communication channels, and a commitment to constructive feedback loops.
Adapting to Change
Adapting to change is a fundamental element in cultivating resilience and agility within the operational landscape of the Maximo Maintenance System. The ability to adapt to evolving circumstances, market trends, and technological advancements is imperative for staying competitive and relevant. The key characteristic of adapting to change is flexibility, foresight, and a willingness to embrace innovation. By embracing change, organizations can proactively respond to market shifts, customer demands, and industry disruptions. However, adaptation to change necessitates a culture of experimentation, risk tolerance, and a mindset that perceives change as an opportunity for growth and innovation.